What kind of foundation you will build, so much a house and it will stand. Therefore, take your choice seriously, to guarantee the construction of a long life. Monolithic foundation is suitable for construction on problem soils, since there are no weak joints in the structure, as in prefabricated bases.
There are 3 types of base made of monolithic concrete. The choice depends on the weight of the structure, the type of soil and your budget. Pour monolithic foundation with their own hands is not so difficult, especially a slightly depressed band and slab.
1. Tape.
Underneath all the bearing walls of the future construction, a strip of concrete is made. It can be shallow (30 -70 cm) and recessed (1 m or more). With a high level of groundwater in clay soils, it is essential to deepen the foundation below the freezing line of the soil, strengthen and isolate it from water. This is the best variant of the basement of the house with a basement.
2. Columnar.
The most inexpensive, the entire foundation - the pillars at a distance of 1-2 m. Suitable only for one-story light buildings on fixed soils. Sometimes this technology is combined with a tape to make a small basement.
3. Plate.
The foundation plate is easy to calculate and fill. Just like the tape, such a foundation is not deep and deep. The first option allows to save considerably on the amount of land works, but does not allow to equip the premises under the house. But you will immediately have a rough floor. The second type is suitable for a heavy structure, in addition, there you can make a basement. But the cost of such a plate is high.
When it is advisable to use:
- Problem soils.
- For houses from heavy materials (concrete, brick, stone).
- For buildings on flat terrain.
Suppose you have already carried out all the necessary calculations, having carried out an examination of the soil and having calculated the weight of the house, and drew a diagram of the future foundation. Technology monolithic plate foundation is simple, so if you want to just fill it yourself.
1. We will outline the area of the future house according to the scheme.
2. Remove the primer and level the surface. The optimum thickness of the monolithic slab is 20-40 cm, depending on the soil and the overall weight of the structure.
3. We fall asleep sand, well we compact. To do this, it is better to moisten it, if possible, use a plate compactor for ramming. Then fall asleep rubble, the thickness of each layer - 10-15 cm, depending on the availability concrete preparation and soil characteristics.
5. We will erect concrete preparation. Lay the film on the surface, so that the liquid does not go into the sand, Usually use the brand M50-M100. The thickness is 5-10 cm.
4. Mount the necessary parts of the water supply and sewerage. It is better to install boxes above the pipes, this will protect the structure from destruction.
6. Put the materials for waterproofing. Their size should slightly exceed the area of the future foundation slab, and all seams need to be soldered.
7. We lay down the layer of thermal insulation.
8. Mount the reinforcement.
9. We install the formwork.
10. Fill the concrete and compact it. It is more convenient to use a vibrating packer to distribute the concrete evenly and quickly over the entire formwork.
11. Cover with a protective diaper. We are waiting for 3-4 weeks, until the concrete will gain sufficient strength for further work.
1. Why do we need stiffeners?
The stove is not always flat. For heavy structures and problem soils, stiffeners are installed under the bearing walls. Most often they are rectangular or they decrease to the bottom. This design increases strength. The ribs placed above the slab make it possible to create a technical basement of a small size, which will simplify the communication in the house. But then the surface of the monolithic foundation slab will no longer be the rough floor.
2. What is waterproofed?
Polyethylene film with a thickness of 200 microns or roofing material. There are special materials for concrete, for example, Delta MS. It perfectly isolates from water, and if the UGW is small, it can play the role of concrete preparation. Also geotextiles are used for this purpose.
3. Is it necessary to insulate a monolithic structure?
Yes. Concrete conducts heat well, and a large amount of reinforcement creates bridges of cold. Common insulation - polystyrene foam and polystyrene foam.
4. Do I need to drain?
Unambiguously needed, if the site is high HGV. It is important to observe the slopes of the pipes, provide a place for the removal of water, make wells, so that in case of siltation of pipes they can be cleaned. Drainage is usually placed in a geotextile on a sand and gravel pillow.
5. How and from what to build a timbering?
We recommend using laminated plywood. It will be easy to remove such formwork. If you make it from ordinary boards, plan them where they will touch the concrete. In the formwork there should be no slots, and its strength is checked by kicking. There are many mixtures that lubricate the formwork to make it easier to remove it, for this purpose you can fix the film on it. Fasten the formwork better with self-tapping screws, not with nails.
6. How to reinforce correctly?
For a slab of 20-40 cm, 2 layers of reinforcement are sufficient. The horizontal distance should not exceed 20-30 cm. The distance to the boundaries of the concrete slab is 15-20 cm. For fastening the reinforcement is connected with a wire. Monolithic reinforced concrete foundation will withstand the load of a two-three-story house made of concrete, brick, stone. For reinforcing bars suitable for diameters of 10-16 mm, depending on the weight of the house.
7. What can you save on?
If you plan to build a porch or a large terrace, do it there band foundation, so as not to waste concrete, since the load on this part will be several times less.
Major mistakes in construction
1. Wrong care. According to the instruction, concrete needs 28 days for a set of brand strength. Especially important are the first days, if dry and sunny weather is, cover the concrete with a tent and water it with water. The optimum temperature for hardening + 15-20 degrees.
2. Low brand. For the construction of a monolithic base, concrete above M200 is required, and if the ground is problematic, it is higher than the M300.
3. Weak formwork. A weak structure will expand under the pressure of the mixture, because of this concrete is not enough. Such an error can not be corrected, the ground will have to be demolished and rebuilt, as it is obligatory to fill everything in one go. If you decide to build yourself, it's better to show the formwork to a specialist.
4. Insufficient heat and waterproofing. High brand and strong reinforcement will not save from cracks, especially for the foundation in the flooded areas, and heating costs will negate the savings in thermal insulation.
5. Wrong reinforcement. Bind the rods to overlap each other by 10-20 cm depending on the diameter. In a monolithic reinforced concrete structure, reinforcement prevents stretching, and concrete - compression, so strength is achieved by a harmonious combination of components.
6. Porch. It happens that developers forget about the porch. But it is better to do it immediately, so that when shrinking into the soil, the house and the porch do not part.
If you decide to build on your own, make the calculations in advance and draw a diagram to choose the correct type. There is no universal monolithic construction, suitable for any case. Follow the technology of building the foundation step by step, so as not to correct their mistakes.
Plate foundation is the most solid and reliable foundation of all known species, but it is also the most expensive. The high price of such a foundation is due to a large amount of costs for concrete and insulating materials, because the size of such a foundation is equal to the dimensions of the base of the house.
The foundation plate. Pros and cons of the slab foundation of the house
Pros for construction
- The indisputable advantage of the slab foundation is that it makes it possible to build, in general, any building (a heavy house, a bathhouse, etc.) even on wetlands or peat bogs.
- The construction of such a foundation, which is a monolithic reinforced slab, allows it to "float" on the soil surface, moving along with a migrating top layer of moist soils. For this feature, the slab foundation was called floating.
- The difficulties of erecting a slab foundation are, as a rule, connected with the moment of calculation of the required materials.
- Such a foundation- solid plate will become a floor for the basement of the house, which is convenient and practically profitable.
Disadvantages of a monolithic slab in the foundation
- Of course, this is expensive, not everyone can afford it. And although the slab foundation is the most expensive of all, there is no need to save on its erection, because the strength and durability of the entire structure depend on its strength.
- If you suddenly want to move the frame house, the foundation is worthless, unlike, which you can unscrew and use again.
Erection of the foundation. Stages of installation
1. The slab foundation is a shallow form of a foundation. After the main marking, a trench is digging on the site of the structure. Plate foundation is arranged in such a way that it does not strongly protrude on the surface of the soil. The depth of excavation is calculated based on the following dimensions: height of the foundation (20-40 cm) + height of the sand cushion (not less than 10 cm) + layer of insulation (up to 10 cm).
We fall asleep with sand. Align the base
2. A sand layer is poured onto the bottom of the excavation, which must be carefully tampered with. Some builders fall asleep a layer of rubble, but this is not necessary, it will still fade into the sand. A foam complex is also not necessary, but firms make more money with it. Then put a layer, which can be used as a ruberoid, overlapped and overlapped by a gas burner. Depending on the climate, a thermal insulation material (foam or) is laid on the waterproofing layer. You should know that this foundation requires insulation not only at the base of the plate, but also on the sides of the structure.
3. The next stage is the erection of the formwork along the entire perimeter of the future monolithic foundation slab.
The formwork boards are also covered with waterproofing.
4. Further on the whole surface of the foundation in the form of a lattice is laid the reinforcing cage of rods with a diameter of at least 12 mm. The bars are fixed with each other by wire, the size of the windows obtained after the ligament can be 20 by 20 cm or 30 by 30 cm.
Preparation of the frame before pouring concrete
5. When the reinforcement frame is installed - fill the concrete mixture. A monolithic slab foundation will require a large amount of concrete mix.
If you can not fill the slab in one step, you can not postpone the filling of the second layer for a period of no more than 12 hours, otherwise the foundation may not turn out as strong as one would like.
We fill the slab foundation with our own hands
There is one more option for erecting a slab foundation, when all around the example of the formwork are placed ready reinforced concrete slabs, which are poured concrete screed. However, such a version of the foundation will be inferior to the monolithic in strength. In addition, the installation of heavy concrete slabs will require the use of special equipment, which is unlikely to be more economically advantageous than the construction of a slab foundation of monolithic construction.
Once the concrete has solidified and gaining strength - the foundation for your future home is ready.
The construction of a single-storey house with its own hands on the stove attracts with its simplicity, ease in implementation. And although not always this type of construction can be called a good choice, it has a number of advantages.
In some cases, a solid monolithic foundation can become practically a non-alternative option, in some cases it is the most successful choice. There are many factors that need to be considered when deciding on the task of drafting a project.
Advantages and disadvantages of the slab base
In reference books and textbooks for architects, a slab foundation is recommended to be used for non-responsible buildings. The reason for this - the design flaws.
From these facts it can be concluded that the slab foundation of the house is an irrational waste of money in the construction with their own hands. However, before deciding, let's enumerate the merits of the design.
- Huge supporting area. According to this indicator plate construction there is no equal. Accordingly, if it is necessary to erect a construction on weakly bearing soils, then there are simply no alternative designs.
- Easy to bookmark. Moderate volume of excavation, simple formwork, ease in site preparation and pouring.
Rigidity of the structure. By this parameter, this variety is second only to the buried band foundation.
Correctly designed support ensures no deformations, so it is well suited for structures with their own hands from a brittle material, prone to the formation of cracks - aerated concrete, cinderblock, etc.
Simplicity should not be misleading. Any shortcomings and errors during the laying will lead to the formation of cracks and serious problems with the house.
We struggle with shortcomings
There are several techniques that allow you to eliminate design flaws or at least reduce their impact when doing the work yourself.
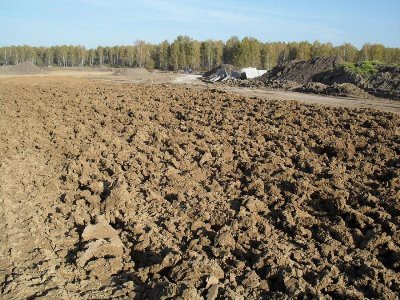
The expediency of using these or other methods is decided depending on specific conditions.
It is also worth remembering that cottage has a moderate pressure on the support, respectively, the factor of uneven load distribution is secondary.
An alternative for a very heavy house, stone, for example, can become a more durable ribbon foundation. For easy construction of elastic materials, not prone to cracking, you can use a pile screw type of the base.
If you still chose the plate variety, then the algorithm of bookmarking with your own hands will be the next.
Sequence of the plate
The slab for the house can lie on the surface of the ground or be buried in it. In any case, the sequence of works is as follows:
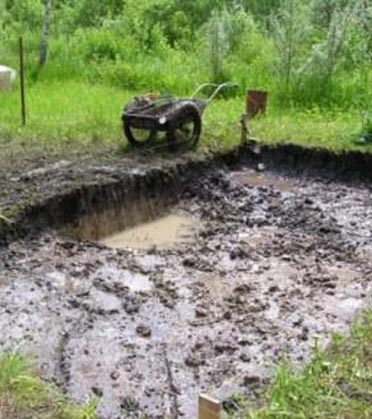
Conclusions and costs
Although in the textbooks for civil engineers, the slab is served as an unreliable basis, modern solutions allow it to be effectively used in the construction of a single-story house with their own hands. But the cost of laying such a foundation is not modest.
More detailed analysis of costs in the article. Accordingly, to choose a similar construction when building a house with their own hands is only when there really is a need.
After the type of foundation for the house has been chosen, the location and depth of its foundation have been determined, all land works have been completed, one can proceed to the last one important step foundation foundation - pouring the foundation slab.
Filling the slab under the foundation with a ready mix in mixers
The fastest filling option, which among other things provides very good quality concrete - order the delivery of concrete in a local construction company. Delivery is carried out in mixers. Usually at a time you can deliver about 6-8 cubic meters of ready-mixed concrete. In this case, the house can be for several hours. It will take about 4-5 people to work. From the mixer, concrete is fed into the trough, which has a length of about 1.2-1.5 m. If the mixture is fed into one place, then it will be very difficult to rake it all along the formwork. Secondly, concrete can begin to separate: a mixture of more liquid begins to pass into the furthest parts of the formwork, and a more rocky dense part will settle in the place of pouring.
Therefore, the mixture must be sent to different places of the formwork, so that it is easier to distribute it over the entire surface. To do this, it should be possible to access the mixer from all sides the foundation. If this is not possible, a long channel is made in advance to feed the concrete mixer from the mixer to different points in the basement. You can beat it from the boards. Linoleum or polyethylene film is placed inside the gutter. Alternately, moving this trough to different corners of the basement, it is possible to ensure uniform filling of the formwork. This option of pouring a slab for most independent builders is the most acceptable and has an average cost: not too big and not too small.
Back to contents
Filling the foundation under the house with a concrete pump
Calling a concrete pump is the most expensive option for pouring. The concrete pump includes a special sliding boom with a concrete pipe, with which a concrete mixture is delivered from 30 to 50 m. Thanks to this, with the help of a concrete pump it is possible from a great distance, even when access to it is impossible for any reason. Concrete pumps are usually used during the construction of large reinforced concrete buildings and structures, but when building dachas, they are usually not used because of the high cost.
Back to contents
Self-pouring foundation under the house
The most budgetary option is to prepare a concrete mixture with your own hands immediately on the construction site. To do this, you can use ready-mixed concrete mixers, with which to knead the concrete mixture is much easier. Concrete mixers operate from electricity and have a power of 200 watts and above. During one batch, you can make from 50 to 200 liters of concrete mix. Using this device will significantly speed up the process of mixing all components and improve the quality characteristics of the mixture. You can do without a concrete mixer and make it into concrete in a barrel or a bathroom. In this case, the kneading is done manually using a shovel.
Using even the smallest concrete mixer with a working volume of 50 liters for pouring 1 m² of concrete, it takes about 20 working cycles. Mixing time for the foundation is 3-5 minutes. It will also take time to deliver sand, gravel, cement and water to the concrete mixer, and then take the manufactured concrete mixture for pouring to the foundation. One cycle will take about 10-15 minutes, that is, one cube of concrete can be poured in 5 hours. If the work is coordinated and involved sufficient number people, then everything can be handled and faster: someone will bring materials, someone make a mixture, someone will pour it into the formwork and compact it.
The building materials and the concrete mixer should be located as close as possible to the foundation to be poured, so that there is no need to carry the mixture far and spend time and effort. For convenience, various shovels and buckets are used for wet and dry materials. Otherwise, dry sand and cement will begin to remain in buckets and stick to a damp tool.
Whatever it was, it was not possible to manually fill in the foundation in one day, especially with large volumes. The fill should be done in parts. In this case, there are two options:
- If the fill should be interrupted for a short time (up to 12 hours), then there is nothing to worry about. The part of the foundation is poured - a layer of a certain thickness along the entire formwork, then a pause is made, the concrete should be covered with a film or roofing felt. From the concrete surface, the next day, concrete milk is washed off (if it comes out on the surface) and the foundation is poured. This joining of layers is called a hot seam (the method of pouring, in which the layers of concrete do not have time to harden).
- If the pause between the fillings is more than 24 hours, it is necessary to make a cold seam: lay a new layer on the previous layer only after it has hardened. Do not lay the new layer on slightly hardened concrete in any case, because it has solidified on the one hand, and on the other hand it only gains strength and can not withstand the pressure of the new layer. As a result, when the new layer is poured, the crust on the old layer is destroyed and a very fragile crumbling area appears on the joint site. From this it is worth to conclude that if the pouring can not continue in the shortest possible time, it is better to finally dry and gain strength to the first layer of concrete.
Back to contents
How correctly to divide the foundation when pouring in parts?
You can pour the entire foundation, but only half the entire height. You can mount the vertical partitions and the foundation pour half, but at full height of the formwork. Some experts believe that it is better to make an inclined seam, that is, put the septum at an angle. In official documents there is no unambiguous answer to this question. This is most likely due to the fact that the pouring of the foundation in parts by professional builders is not considered correct. However, this does not mean that if you build a low-rise house on your own, you can not do it. After all, the requirements for the strength of the foundation created in this case are not the same as when building a high-rise building.
Do not make a horizontal seam in the place where the horizontal rod of the reinforcing bar passes. It will be better if the armature will be located in one layer, and not at the junction. Do not make the layers too thin: when pouring the foundation in small portions it is better to do vertical seams, and not horizontal.
Back to contents
Features of the technology of pouring the slab under the foundation
Parameters of a monolithic slab and its thickness are defined in the design of the future building. If the structure is sufficiently light (for example, when building a garage), the minimum thickness of the plate will be about 100 mm. When building a suburban one-storey house it will be necessary to create a plate with a thickness of about 200-250 mm. Too much increase in the thickness of the monolithic slab is not advisable, as the unstable soil will increase its load and the main advantages of creating such a base will disappear.
As with the creation of other types of monolithic foundation, when pouring a slab, it is necessary to carry out a complex of works on waterproofing. Protect the slab from moisture is necessary on all fronts:
- The waterproofing in the lower part of the structure is made using roll materials even in time. Preference should be given to bitumen-polymer materials that are lapped over after a sand pillow has been prepared. Between the sheets joints are sealed by the method of fusing the edge of the waterproofing material with a gas burner. It is also necessary to leave a stock of material in advance to protect the ends of the plate.
- Waterproofing of the side parts is made due to the waterproofing materials of the sole.
- Waterproofing of the top surface of the plate is made with roll, coating and spraying building materials.
In order to reduce heat loss, the base plate must be insulated with a variety of materials. Most often, warming is used under the foundation, which involves placing the slab on a layer of thermal insulation. Even more effective is the use of thermal insulation in the installation of floors - directly under the screed. As a heat insulation material, polystyrene or foam is most often used.
For the manufacture of formwork boards with a thickness of about 25 mm are used. Of these, shields are knocked down and installed around the perimeter of the future plate, fixing the construction with pegs and struts.
To create the reinforcing cage you need to use steel ribbed rods with a diameter of about 12 mm. The diameter of the rod is selected based on the loads on the foundation to be created and on the nature of the soil. The binding of the reinforcement is made by welding or wire. When choosing concrete, it is necessary to give preference to mixtures with a grade not lower than M-300, which have a strength class of 22.5.
It is economically justifiable to construct a slab foundation with unsatisfactory load-carrying capacity of the soil in the building spot, high UGW, high clay content, swelling during freezing. Construction by own hands of a plate is possible on an equal site at the guaranteed absence of external communications.
When specifying the main drawback of the slab base - high cost, the opponents of this technology do not take into account that the slab is also an overlap, a floor on the ground, allows integrating the heating system into it. This, in the long run, is cheaper than a deep tape base, the amount is quite comparable with MZLF with a safety margin of 300%.
The scheme of the pie protected from frost whipping of the slab of a private house has the form:
- sand - 15 - 20 cm, replaces the abrasive soil;
- crushed stone - 15 - 20 cm, is a draining layer;
- communication - necessary for life support systems;
- drainage - laid along the perimeter, collects water from the ground, removes it from concrete structures;
- concrete preparation - a thickness of 5 - 10 cm, is used as a rigid base for a roll waterproofing, which in its absence will be torn with sharp corners of the rubble;
- waterproofing - two-three-layer, roll materials are recommended on a polyester, fiberglass base (Technoelast, Linocrom, Bikrost), the layer protects the concrete structure from moisture;
- thermal insulation - 15 - 30 cm, preserves under the sole of the house geothermal heat of the bowels, the puchynisty soil does not freeze, the strength of the whipping is absent;
- stiffeners - increase the strength of the slab, are made across the long wall of the house and along the perimeter, pointing down from the sole;
- armopoyas - two reinforcing mesh with a 20 x 20 cm cell of 12 - 16 mm rods;
- warm floor - water contours, laid over the reinforcement or between the nets;
- concrete - thickness 20-50 cm, provides rigidity, strength of the plate;
- flashing - from expanded polystyrene, protects the plate at the ends;
- thermal insulation - sheets of expanded polystyrene increase the perimeter of thermal insulation, cutting off lateral freezing.
The main advantages of the slab foundation are:
- absence of special equipment - all the work can be done by one's own hands;
- minimum excavation - it is enough to remove the fertile layer.
The main costs are for the reinforcement, insulation, waterproofing and ready-mix concrete, which is better ordered for guaranteed filling of the formwork in one step.
Step-by-step instruction for the construction of a plate foundation
Step-by-Step Scheme of the Plate Base Device
Research and calculation
Soil sampling
When designing a monolithic slab, it is necessary to take into account the experience of similar structures in the region, the results of surveys (GW, the nature of the soil, the bearing capacity of the formation), the terms of reference (storeys, roofing materials). Research includes at least five geological pits (corners + middle of the slab).
The result of the survey is the characteristics of strength, deformation of different layers of soil in the building spot, predicting changes in the chemical composition during the operation of the dwelling, and the degree of aggressiveness of groundwater.
It is necessary to compare several solutions to identify the best combination of the construction budget, technical specifications. Step-by-step calculation instruction:
- concrete grade - M200 and higher for the slab, M50 for preparation, according to the foundations of structures, buildings;
- the depth of the UGW - anti-corrosive measures in the presence of perchovodki;
- when calculating prefabricated loads, the weight of the slab is not taken into account on sandy ground;
- the load-bearing capacity, deformations capable of destroying the structure are calculated.
For this purpose, special programs are used, which proved the operability of the foundations made under their results in real operating conditions. The main documents at this stage are:
- soil classification -;
- fencing, bearing structures -;
- anticorrosive power frame of the building -;
- design, manufacture.
Unlike tape bases, the plate has an increased support area, prefabricated loads from the building are distributed evenly, the strength stock is very large.
Marking and excavation
We remove the fertile soil layer
Plate is forbidden to fill on the fertile layer. The layout of the house looks like this:
- axes - are carried out in the building spot by a cord fixed on pegs installed further than the perimeter of the drainage system;
- the foundation pit is 0.5 meters larger than the slab on each side (for the drainage device), the slab stands for the dimensions of the building by at least 10 cm (depending on the project).
In view of the small amount of work to remove the fertile layer (20-40 cm) for a residential house, the work is done by oneself without the use of special equipment. At this stage, it is necessary to protect the monolithic structure from soil moisture (perchage). For this, drains are placed along the perimeter:
- geotextile entering the edges of the ditch;
- layer of compacted rubble;
- perforated pipe (corrugated or smooth in a dornite filter) with a slope towards the underground reservoir;
- backfilling with a natural filter (crushed stone of fraction 10/20);
- shelter with the remaining geotextiles.
Do not install drains under concrete preparation or base plate. The height of the backfill should be level with the crushed rock foundation pad.
In addition, after filling the slab in the building, it is impossible to enter the communications, so the pipelines of the HVS, the sewers are laid at the same stage. They do not necessarily bury below the freezing mark, as the heat insulation of the soleplate will preserve geothermal heat, the ground will not freeze under the cottage. It is sufficient to have a depth of 1 - 1.2 m.
Substrate
We arrange a sand pillow. Sealing is mandatory.
Another measure to reduce the strength of the bundle is the substrate. It is made by the hands of the technology:
- layered compaction of sand - 10 cm backfill, abundant moistening, tamping with a vibration plate, second layer of similar thickness;
- layered compaction of crushed stone - fraction 10/20, similarly.
We lay a layer of rubble.
Instead of rubble, sand, a mix of PGS can be used to a depth of 40 cm with compaction by this method. Only in this case monolithic base at home will receive reliable support on the lower stratum.
Concrete preparation and waterproofing
We make concrete preparation.
For a monolithic slab, a lower waterproof cut-off is required, which prevents corrosion of concrete and reinforcement inside it. Laying the carpet of waterproofing from rolled materials along the bed of crushed stone does not satisfy the operating conditions:
- sharp edges of stones break through the material;
- seams can not be sealed properly.
Therefore, when building the foundation of the house with their own hands, concrete preparation is often used. This is an ordinary screed, which solves two problems:
- providing a flat surface on which it is easy to paste the bituminous base of Bikrost, Linocrom, Technoelast, seal seams reliably;
- the creation of a flat base plate, strengthening its strength, stabilizing the geometry.
We lay waterproofing.
The method of pouring into the formwork is standard, the thickness of the screed is 5 cm, reinforcement is not required. Roll materials provide a minimum budget for construction, impregnation, primers are not used here. The recommended overlap of the strips is 15 - 20 cm, the seams are treated with hot or cold mastics on a bituminous basis. The edges of the waterproofing carpet are released behind the perimeter of the concrete preparation, so that after pouring the slab, run them on the sides and top surface.
We lay the heater under the entire area of the building.
As an insulator, extruded polystyrene XPS is used. It fits in two layers (10 + 10 cm) closely for smooth slabs. If the project provides stiffeners, the first layer is laid by hand, but the second one creates gaps along the width of the ribs:
- along the perimeter;
- perpendicular to the long wall after 3 m.
In this case, a monolithic slab has a large margin of safety, the house is free from distortions during operation.
Reinforcement
We create the reinforcing cage in accordance with the project.
The reinforcement of the plate by armo-bands is made, according to the normative documentation for reinforced concrete, concrete structures. the reinforcement scheme looks like:
- the production of clamps is a smooth 6 mm rod bent in the form of a square, a triangle;
- creation of reinforcing mesh - longitudinal, transverse bars of periodic profile with a diameter of 12 - 16 mm, knitted by wire or welded (cell 15 x 15 cm);
- reinforcement of the stiffeners - four longitudinal bars connected by clamps;
- laying of the lower belt - is installed on concrete pads (thickness 15 - 25 mm, section 10 x 10 cm) to provide a protective layer (the reinforcement must be recessed into the concrete);
- installation of the upper belt - on the lower grid are placed clamps, on which the top card is attached.
From the ends, the plate is reinforced with U-shaped clamps.
It is not advisable to use individual rods inside the armpole. They need to be bent in curvilinear sections, in places of communication input nodes with common mesh maps. To save the reinforcement, the cell in some cases is enlarged to 20 x 20 cm.
Decking
We install and strengthen the formwork.
To fill the monolithic structure with your own hands, a formwork must be installed along the perimeter. It is built of OSB, chipboard, plywood or edged boards in the form of shields. The inner surface is covered with a roofing material or a film to exclude the chipping of the concrete during stripping. The main document in the construction of the formwork are standards; .
Shields are mounted around the perimeter, to protect the structure from freezing inside them, 10 cm of polystyrene foam can be laid vertically. Under the blind area of the house, this insulation is also laid to prevent side freezing. It is laid at the level of the soleplate, flush with the bottom or top layer of the thermal insulator inside the formwork.
Pouring and care of concrete
We pour concrete into the formwork and level the surface. Sealing is mandatory.
Requirements for the design, manufacture of MLF are specified in the regulations, according to which the work is carried out. When pouring it is necessary to fulfill the following conditions:
- filling formwork with concrete in one step;
- the maximum interval between mixing with the mixer after vibration of the previous section is 2 hours in warm weather;
- it is forbidden to distill concrete with shovels all around the perimeter from one place - it is necessary to rearrange the mixer or use a concrete pump;
- vibrocompaction is made before the appearance of cement milk, the concealment of rubble and the absence of bubbles;
- the step of lowering the nozzle of the deep vibrator can not exceed its range;
- in winter, the heated mixture is heated by a cable laid inside the casing, covered with film materials, heated by steam;
- the vibrator tips are forbidden to rest against the arches of the armpoles;
- the decking is possible on the fifth - seventh day in normal conditions;
- a mirror of concrete must be protected from rain, should be covered with burlap, wet from a watering can in the heat.
With respect to technology, recommendations for the selection of materials, sections of the reinforcement plate foundation will not require restoration, will serve three generations of property owners, at least. All these technologies comply with the requirements of these normative documents, they have operational experience in the regions of the Russian Federation.
Advice! If you need contractors, there is a very convenient service for their selection. Just send in the form below detailed description works that need to be done and to you on the mail will come offers with prices from construction teams and firms. You can see reviews about each of them and photos with examples of works. It is FREE and does not bind you to anything.