The quality of the garage is predetermined not only by a sealed roof, reliable walls and gates, but also by the presence of a floor. On how well the floor for the garage is qualitatively depends, both the convenience of setting the car, and the accompanying repairs. Owners of car boxes, can not decide on the optimal floor surface, puzzling with the question "what kind of floors is better to have in the garage"? In this regard, it is worth noting the following most common options, based on the applied building materials:
- earth;
- concrete;
- wood;
- paving stones;
- ceramic facing;
- loading floor.
The presented variations of garage floors are most common among motorists who have their own autobox. The article will give an idea of which floor in the garage is better to perform.
The option is simple in implementation. Used in cases where there is no time to qualitatively equip the garage area.
H3 Advantages
As a temporary option, the earth surface will be a digestible way to make the box area neat.
The advantages of such a floor in the garage include the following items:
- minimum costs in a financial sense;
- does not require special knowledge and skills in its design;
- time to perform is minimal.
H3 Disadvantages
Negative moments for this type of sex more. Using the garage, the owner will have to deal with them from time to time. In particular:
- there is a lot of dust (especially in dry weather), so keeping the car clean is a burning, painstaking task;
- dirt in rainy weather from drops of water draining from the body and wheels of the car;
- in the cold months of the year it will draw cold;
- lack of possibility to conduct insulation;
- constant podsypka and compaction of soil in the places of formation of the track with frequent entry / exit of the vehicle.
H3 Manufacturing technology
The whole process is divided into two stages: preparation and direct execution. At the first stage it is required to release the garage area from the construction debris. It is necessary to remove a layer of fertile soil in order to exclude the further germination of grass, which in consequence can make the compacted surface uneven. Sufficient will remove 15-40 cm of the soil layer. To exclude the possible germination of grass, the entire surface of the room is covered with thick polyethylene film.
Further, the first backfill is carried out with a clean primer up to a thickness of 50 mm. To compact the backfill layer, tamping is carried out by means of a vibrating platform. In the absence of such equipment, it is possible to make self-tamping device, taking a small chock, and nailing to its upper surface a piece of wooden bar, which will serve as handles. After falling asleep each layer requires another rammer. The floor of the garage must have a slight slope towards the gate for water leaving to the street.
H2 Concrete floor
Many who have encountered the question "what better to make the floor in the garage" prefer concrete surfaces. The variant makes it possible to further refine the surface by means of other construction and finishing materials, or to conduct insulation with subsequent finish, for example, tiles.
H3 Positive aspects of concrete coating
It's nice to have a firm and level surface under your feet. The option is appropriate for capital construction.
Concrete floors have the following advantageous features:
- strength for many years;
- are not afraid of high humidity and temperature drop;
- the possibility of washing not only the car within the box, but also the floor itself by means of hose watering.
H3 Negative moments
Despite the obvious advantages, concrete pouring stops some owners of garages from its implementation due to certain reasons:
- labor intensity of work;
- it is necessary not only professional skills, but also special equipment, so that the preparation of the concrete mixture is faster;
- carries a significant financial cost for the purchase of cement and sand.
H3 How to make a concrete floor in a garage
The process requires compliance with the filling technology, in which a number of sequential actions are performed:
- removes 20-30 cm of soil inside the room;
- the area is poured with crushed stone for a thickness of 10 cm, followed by leveling;
- a sand pillow 10 cm thick is arranged, leveling and tamping is performed;
- screed with a thickness of 2 cm is made of sand-cement mixture;
- spreads waterproofing in the form of ruberoid;
- folding reinforcement mesh based on steel rods is stacked (the optimal size of the cells is 15 by 15 cm);
- the main pouring of a concrete layer 5-7 cm thick is made.
This work does not end there. Requires periodic watering of the concrete surface to prevent uneven drying, and hence cracks in the floor.
H2 Floor on the basis of paving slabs
How to make the original floors in the garage? Pursuing this goal, a certain part of the car enthusiasts uses paving stones. The material is produced on the basis of a sand-cement mixture. The thickness of the laid paving slab is adequate to the layer of pouring of the concrete floor (70 mm).
H3 Sidewalk Stone: Advantages
The material is marked by such advantageous properties as:
- strength (the floor withstands significant mechanical stress);
- originality and color of the overlap (you can use material of different colors).
H3 Negative aspects
Sidewalk stone is a good construction and finishing material for transforming the space of the auto box, but it has its own disadvantages:
- relative high cost, in comparison with the same wooden board;
- additional costs for acquiring the necessary associated construction materials (crushed stone, sand);
- strict adherence to the technology of laying (without professional skills it is not necessary to do the work yourself).
In addition, not having met the standards for laying pavers, the coating may eventually have depressions in the places where the car is set up.
H3 A set of measures for laying pavers
The technological process boils down to the following stages:
- removal of the soil layer (thickness 20-30 cm);
- the application of a gravel cushion up to 10 cm thick with subsequent alignment;
- sandy filling (thickness 5-7 cm) with obligatory tamping.
After the preparatory process is carried out, a layer of sand is poured into 5 cm, and the pavers are laid directly. Performing a mosaic of stones, you should carefully fill the gap between them through sand.
H2 Floor of boards
Choosing the floor options in the garage, the most optimal, based on the criterion of "price-quality", is a wooden floor. It is executed on the basis of a floor strip or a planed board with a thickness of 50 mm.
H3 Positive factors
Professional builders have the following positive properties of wood use:
- ecological cleanliness;
- longevity (if larch is used, the service life is several tens of years in a row);
- simple installation process;
- inexpensive building materials available to a wide range of owners of autoboxes.
In addition, the flooring acts as a kind of warming layer. The property is especially important in the cold season (the room does not so quickly protrude).
H3 Cons
Due to the properties of wood, this type of garage floor has its negative side:
- can be a source of fire or support it;
- absorbs moisture, which leads to the formation of organics in the wood structure, as a result - rot.
If these disadvantages are not critical, then you can make the floor by means of boards. This option can be called "cheap and angry".
H3 Decking process
For a wooden floor, you need to purchase the required number of boards with a thickness of at least 40 mm, as well as bars, which will act as lags. Technical operations will be done as follows:
- chipping the horizon of the future sexual surface by means of a laser level;
- layout of bars with observance of a standard step between them in 40 sm that will exclude superfluous loading on separate boards at arrival on them of the car;
- the device boards, and fixing them to the lags.
A little advice. Instead of the classical nailing of racks (boards) by means of nails, it is advisable to use self-tapping screws, which should be "pinched" under a slight slope with respect to the horizon of the boards, which will better affect the close fit to the lags. At the end of the installation, the floor is impregnated with an antiseptic liquid.
What kind of floor is better to do in the garage - it's purely individual. Despite this circumstance, it is important to be pragmatic not only to the option of sex, but also to the technological process of construction.
The basic requirements for flooring in the garage, various options for materials for installation in the garage, their shortcomings and advantages, the rules for pouring concrete screeds, the recommendations of specialists in laying floors.
The content of the article:
The floor in the garage is a coating that should not dampen and emit a lot of dust. Undoubtedly, the main requirement is that it must withstand heavy loads. Thus, the car will be stored in a well-equipped place. The classic floor covering in the garage is a concrete screed, but today materials such as wood, tiles, as well as earth and self-leveling floors are popular.
Requirements for floor carpeting
If you decide to independently install the floor covering in the garage, the main problem is the proper selection of materials, because the assortment in building stores is huge. In addition, to date, there are many technologies with which you can make various floor bases.
Garage room - a kind of place, and the floor in it must meet certain requirements:
- The coating should be durable and reliable, withstand permanent loads and external mechanical stresses. From the mass of the car on the floor should not appear dents, cracks, scratches or other defects.
- Resistance to chemicals. Often a garage is used as a workshop, where motorists can repair the car on their own. And in this case, the floor material must also be resistant to the effects of various chemicals.
- Easy to clean. It is important that it is easy to take care of the floor in the garage, because it is polluted regularly.
- Resistant to fire. If the base of the covering is a tree, then, of course, it is far from safe in this respect. In addition, fuel and lubricants (fuel and lubricants) will also be harmful to such a floor. Wooden cover for this indicator - not the best option for styling in the garage. If you still chose the wood, then before starting work it must be impregnated with special solutions.
- Moisture resistance is an important requirement, since in the winter and autumn period a lot of moisture gets to the floor from the wheels of the car, which eventually destroys the structure of the coating and reduces the life of the coating.
Materials for arranging the floor in the garage
There are several most common materials that are often laid on the floor in a garage room. They have special technical characteristics, as well as their shortcomings and advantages.
Reinforced concrete slabs on the floor of the garage
This material is able to make the floor in the garage more durable and stable. But you will not be able to lay the plates yourself. Better to entrust this matter to professionals or to enlist the help of friends.
Among the advantages of such material for finishing floors in the garage can be distinguished convenience in work and speed of laying (subject to the availability of a team of workers), strength and reliability of the surface.
It is worth noting and certain disadvantages of reinforced concrete slabs as a floor covering:
- Great weight. If you hire a professional team of builders, then it will involve additional expenses.
- If the slabs are laid directly to the ground, then they can soon crack due to subsidence beneath them.
- If the garage temperature is too high, the material can expand, which will lead to the destruction of both the slabs and the foundation of the room. Therefore, it is recommended that first of all, before starting the work, it is good to compact the soil and make gaps between the foundation of the garage and the working material.
The wooden covering for the garage is currently not as popular as it used to be. New materials, methods and technologies have appeared. However, until now, such floors are stil, because they have a number of advantages:
- Wooden floors in the garage are quite relevant, as the installation work can be done independently, without the use of expensive equipment and additional labor. The laying process is fast enough.
- Unlike concrete or brick floors, wooden can keep heat well, they "breathe". And this means that the garage will not have an unpleasant smell of gasoline or chemicals.
- Such a floor covering is inexpensive and environmentally friendly.
- Short service life (in contrast to concrete). Under the influence of constant friction of tires and chemicals, the period of use of this floor will be no more than five to seven years.
- A strong mechanical impact will be detrimental to the wooden floor.
- This coating is easily ignited.
- If the room is wet, then the tree will quickly deteriorate and rot.
- Wood is susceptible to rodents and pests.
Concrete floor screed in the garage
Concrete screed is one of the most popular options for flooring in a garage. And there are many reasons for choosing a cover, since it has such advantages:
- The floor will be very durable. He is not afraid of large and uneven loads.
- The coating is resistant to chemical fluids, oils and gasoline.
- Such a floor is safe, since it has refractory qualities. If there is a fire in the garage, the flame will not spread.
- With proper concreting, the coating will also be waterproof.
- The process of filling the floor in the garage is very simple.
- Long service life of the flooring.
- The process of filling is simple, but rather laborious.
- The floor can get very dirty, it will require frequent cleaning.
- Concrete coating can quickly abrade. The top layer of the pouring is destroyed and turns into gray dust.
- The concrete floor has good absorbency, so any spilled liquid will be difficult to remove. In addition, the unpleasant odor can also be disturbed.
Rubber coatings for garage
Rubber is an excellent material that is ideal for a garage due to its advantages:
- Such a floor covering is distinguished by its durability and strength. Paul will serve you more than fifteen years.
- The rubber floor has increased wear resistance. He is not afraid of sudden temperature jumps, ultraviolet radiation, exposure to fuel oil, acids or alkalis.
- Rubber is characterized by a high level of watertightness, as the flooring has water-repellent qualities. Thus, you can wash the car without leaving the garage.
- The material also has noise-proof and anti-vibration properties. Garage, floor covering which consists of roll or sectoral rubber decking, completely isolates the sound.
- It is very important that such a coating with an anti-slip effect is quite safe. It will not freeze, which will ensure you comfortable walking in any weather and season. Rubber material is not flammable and environmentally friendly.
- Work with such a flooring is very simple, which will allow you to make the floors in the garage with your own hands. Help professionals will not be needed, which means that extra material costs are excluded.
- It is easy to care for such a coating, cleanliness is easy to maintain, no special effort is required. Rubber floor is washed with ordinary water, do not use special detergents.
The latter variety has long been popular and in demand among consumers who want to qualitatively equip their garage. The filler has both pluses and minuses, which are much smaller than the advantages.
Before you fill the floor in the garage, you need to study the technical characteristics and features of the material:
- During the installation, no seams will form. And this means that in the crevices of the floor covering dust will not gather and the bacteria will multiply.
- Rubber filler coating is absolutely ecological, it does not emit harmful substances, it does not harm the human body and the environment.
- The mixture quickly freezes. Some substances need only a day to completely dry out, and they will be ready for active use.
- Self-leveling floors can be insulated.
- They have a high degree of stability. They are not afraid of mechanical damage.
- Will serve the floor for more than forty years.
- This kind of coverage is not yet very common in our country, therefore it has a high cost. But it's worth considering the long service life, for these decades the cost of acquiring the material will pay off exactly.
- The filling process is not very simple. It is long and time-consuming, and it is better to entrust it to a team of specialists. If you decide to fill the floor yourself and make a mistake, then significantly shorten the period of its use.
- The process of dismantling is also not simple. And it is recommended to simply install a new coating over the bulk, so it will be much easier and cheaper.
How to make a concrete floor in a garage
The problem of installation works is that the material will be in tight contact with the soil, which emits a lot of moisture. The levels of the underwater waters can be quite high, and the room can be heated, especially in the spring. This is very important to consider, before making the floor in the garage this most common way.
Do not forget the important detail - the bottom of the floor should be under a slight slope. It is necessary to ensure a qualitative outflow of water from the garage. In this case, you can wash the car without leaving the garage.
Features of installation of a floor from concrete in garage:
- We make a mound of gravel. It will serve as a kind of drainage. Its main task is to remove unnecessary moisture, not allowing it to penetrate into the concrete coating. Do not make this layer more than ten centimeters.
- The next step is the filling of the sand layer, which will also remove moisture from the concrete and transfer it to the lower layer. The thickness of this layer should not be more than one hundred millimeters.
- We install waterproofing, which will not allow penetrating ground waters to the floor of the garage. As a waterproofing we use a dense polyethylene film, which we fix with an overlap of twenty centimeters.
- Fill a concrete pillow (its width should not be more than twenty centimeters). The material can be poured and leveled by eye, but it is recommended to use beacons.
- The concrete interlayer is fixed with a reinforcement of 1 cm. After finishing the work, the floor is covered with polyethylene. Thus, the evaporation of water decreases, the material dries more slowly, becoming much stronger at the same time. The process of complete drying will take several weeks.
- The final stage of laying the concrete floor is the screed. The process should take place clearly, therefore it is necessary to use beacons. The screed must be reinforced, for this we use a metal net. If you add a small amount of liquid soap into the water, the concrete solution will not dry up so quickly.
- At the end of the work, the floor is again covered with a polyethylene film, we remove it only when the surface becomes a light color. This will mean that all the excess moisture has evaporated. To dry the concrete cover will take at least a month.
- To strengthen the concrete surface, it is smeared with a special "milk" of cement in such a proportion: 1 part of the cement to 3 parts of water. Also, add slaked lime or polyvinyl acetate emulsion to the solution.
- If desired, the floor in the garage can be insulated. If you do not want to insulate it with a special system, you can add claydite or pumice to the solution, the surface will become slightly warmer.
Do not lay the ground near the walls under the foundation. At a distance of fifteen centimeters it is necessary to fill in sand, rubber or any other insulation. Thus, if the garage will sink, the floor will not be damaged.
How to make a floor in the garage - look at the video:
The choice of materials for laying on the floor of the garage is very wide. Before buying it is necessary to make calculations, to study technical characteristics. The main requirement is that the floor in the garage must be practical and durable.
This floor is made of wood
The floor in the garage must be resistant to mechanical damage and chemical compounds that are not susceptible to fire and high humidity. How to achieve this? Than to cover a floor in the? All possible options have their pros and cons. Because of what does not stop the dispute between car owners. Which is better in the garage? We will try to answer these questions in this article.
Flooring options
Today, the floors in the garage can be made in various ways. The most popular types are:
- earth;
- concrete;
Consider the merits and demerits of each and the phased implementation of works.
Simpler: earth floor
Advantages of the earth covering:
- almost complete absence of monetary investment;
- maximum simplicity of arrangement.
Disadvantages:
- low strength for wear;
- high humidity (the soil is inherent in absorbing moisture from below).
How to make sex this way?
- cut off completely the vegetative layer (if any).
- align the base.
- it is good to compact it with a rammer.
Advice! To increase the strength of such a floor and provide protection from moisture will help fatty clay. The recommended thickness of the clay layer is more than ten centimeters.
Classic - from concrete
Concreting the floor in the garage - this is the first stage of work in almost any kind of coverage. Also, concrete is an independent coating, quite popular among car owners.
Pluses:
- high strength and resistance to mechanical damage;
- low cost of materials.
Disadvantages:
- dust formation during operation;
- chemicals and dirt eat into the concrete, creating an unpleasant smell in the garage;
- laborious and "dirty" process of pouring concrete.
The device of the concrete floor in the garage depends on the luck of the car owners. If lucky, then as a base there is already a solid reinforced concrete slab. Work on such a floor covering is a pleasure. No trouble. Poured concrete - and that's it.
If not very lucky, then the ground will be the ground. And to pour concrete floor in the garage on the ground, you need to perform several laborious processes:
- Align and tamp the bottom.
- Make a waterproofing layer. To do this, flush the base with liquid clay.
- Run on the walls marking the height of the future floor, pull the rope landmark.
- Fall asleep gravel. The recommended layer thickness is about 80 cm (under unfavorable conditions), about 45 cm (under favorable conditions).
Advice! To indicate the height of the gravel layer, it is possible to install wooden posts along the walls in steps of 1 m.
Gravel is compacted by removing sharp and too large stones. Fall asleep about 10 cm of sand. And also dump it. Thus, each layer of the filter cushion must be carefully pressed. The main condition of the quality of work is also the flatness of the surface horizontally (the permissible deviation is +/- 2 cm).
Waterproofing of the floor in the garage is carried out by means of polyethylene film or modern membranes. Strip the polyethylene with the entire surface, laying them overlap. Joints to work with polyvinylchloride tape. "Start" the film on the walls (just above the level of the finish of the future coating). Carefully smooth.
Strengthen the concrete covering with reinforced mesh. Suitable material with cells 10 × 10 cm and a rod diameter of 0.5 cm. Cover the entire area with a mesh.
Install long wooden slats (1-2 m), the width of which corresponds to the height of the rough coat (10 cm), in 1 m increments. Pour the prepared mortar into strips, in between the slats, so as to hide the beacons. The wooden rule is to remove the excess solution, to the right / left by progressive movements to mix the mixture.
Advice! The concrete floor screed in the garage should not "come up" against the walls and pipes: the structure can shrink and damage the floor covering. Filling the floor, along the walls and near the pipes you need to leave gaps. In the formed slots put pieces of elastic insulation.
Bay "rough" concrete, cover it with a film and leave it for a month. Periodically moisturize.
If you plan to insulate the floor in the garage, the next layer is a heat insulator. Possible variants of the material: mineral wool, foam plastic, penoizol, astrake, ruberoid and others. It is more convenient and faster to work with roll insulators. For waterproofing and vapor barrier insulation cover the top with a film.
Finish filling the floor in the garage is similar to "rough": cover the surface with a metal mesh, set beacons, pour concrete, align and compact. Flatten the surface with a steel smoothing pad.
If there is no insulation layer, then first the black coating is coated with cement "milk" (cement, plasticizer and water), then the "finishing" concrete is poured.
Note! The finishing tie should be done with a slight inclination towards the exit from the garage. This is necessary for water drainage.
To increase the service life, as well as to save the room from dirt and dust, reinforce the top layer. You can use special impregnations or paints. How to paint the floor? Special polyurethane, acrylic or epoxy enamels.
Ecological care: wooden floor
The wooden floor covering in the garage has its advantages:
- ecological compatibility;
- high profitability;
- simplicity of installation;
And cons: short-lived (average life - 5 years). Stages of work:
- Make a rough concrete floor (see above).
- Prepare lags: treat with antiseptic, dry.
- Place beacons in steps of 2 m. Mount each half a meter with dowels.
- Place the intermediate lags in 40 cm steps. Fasten similarly.
- Lay gidro-and vapor-insulating material in the gaps of the frame.
- Secure the floor boards as tightly as possible to each other with nails or self-tapping screws perpendicular to the logs.
It should not be for the sake of economy to install lags immediately on the ground. Such a coating will fail for two seasons.
Motor home with a claim to luxury: ceramic tiles
- water resistance;
- absence of excessive spraying;
- simplicity of cleaning.
Cons: high cost of materials and work.
For flooring in the garage you need a tile with a 5 class of wear. And for unheated rooms - frost-resistant varieties. Only strong building materials will provide high resistance to mechanical damage and abrasion.
In no case can not lay ceramic tiles on the floor of the newly built garage. The coefficient of expansion of this material is too low, so the tile will not withstand the shrinkage of the building in the first two years.
So, we make the floor of the tile:
- Run the concrete screed.
- Prime the surface.
- Apply to the area of the floor with a serrated rule the adhesive composition corresponding to the tile brand. Lubricate the edges of the tile. Lay the material in rows, checking the level with horizontal. To make the seams smooth, you need to use special plastic crosses.
- Three days later, wipe the seams. The floor can be used after 2 weeks.
Self-leveling floors in the garage
Modern leveling solutions can have a cement or polymer base.
Pluses of self-leveling floors:
- high abrasion resistance;
- ideal smoothness and evenness;
- the ability to experiment with color;
- simplicity of installation;
- simplicity of cleaning.
Cons: high cost.
For garages, polyurethane and epoxy industrial floors are more suitable. Such polymer coatings are guaranteed to last more than 45 years.
How to fill the floor?
The flood
Prepare a concrete base: to repair cracks, potholes, to clean from dirt, dust, sand. Apply the primer to the floor surface in two layers, each of which must be allowed to dry. Prepare the solution by following the manufacturer's instructions.
Pour the composition, which is applied portionwise. Pour the solution on a certain area - align with a serrated roller, carefully removing all the air bubbles. Work on pouring the floor is recommended to be carried out at a temperature of 10 ° C to 25 ° C. The limit level of humidity in the garage is 60%.
Thus, each floor has its pros and cons. The choice is for the car owner. If the means permit, you can make a filler floor - the most suitable for a garage on technical specifications. If the budget is significantly limited, then temporarily you can do earth flooring or make a wooden one.
FROM the private car owners, who own their own garage, spend a lot of time in it alone with their own iron horse. The interior finish of the garage in this case should be as neat, practical and comfortable as the finish in your own home. Of course, the floor is subjected to the greatest load. In a huge variety of coatings, you need to choose exactly the one that will satisfy all the requirements of the owner and will prove to be the most durable and economical. The floor in the garage is better - modern materials or rough surface? The answers to the question are in this material.
Floor in a modern garage
Variants of floor coverings
The floor in the garage is subject to extremely intense impact: it drives the car wheels, heavy objects move, and people walk in shoes. In addition to mechanical damages, the floor covering receives also chemical: fuel, oils, acids, paint and other aggressive compounds fall down even among the most neat motorists. Car washing also shortens the life of the floor, if its finish does not match the available loads.
Washing "kuherher" - a serious test
An economical option from bulk earth or sand cover can hardly be called successful for obvious reasons: with such finishing, dirt is inevitable, which will appear in the cabin or at home, especially in conditions of high humidity. Asking the question, what are the best floors in the garage, you can answer that any, except earthen, because they are generally difficult to call the sexes.
Another option - wooden floors - also has more disadvantages than pluses. At a cost, it is comparable with the bulk, and for durability is strong to him inferior. Due to the flammability of such a floor - one of the worst options for garages, where fuel can easily splash out, catch fire and cause this serious damage.
Concrete base: slab and roughing screed
The basis of any floor is a concrete slab or a monolithic concrete block. In the first case, the quality and brand of concrete is checked by the manufacturer, so the factory concrete slab has good strength characteristics and can be used as a floor covering.
Monolithic concrete, which is arranged on site, on strength may be inferior to the slab. The norm for complete hardening of concrete takes 28 days. During this period, the cement compound is protected from drying, constantly watering and preventing evaporation.
Concrete is not just a dried up solution, this substance in which water molecules are embedded in the structure of a stone, it is the moisture content that determines the strength of the finish coat. If the technology is observed, then the coupler will last a long time.
Determine poor-quality coating easily, just with the soles of shoes rub the screed, and if sand appears - the floor should be "brought to mind" by other types of finishing, otherwise it will not last long.
The floor in your garage: it's better to have a stove or screed - it's impossible to answer unequivocally, because you should evaluate the coverage individually in each case.
Related article:
In a separate publication you can find out where this type of screed is applied, what advantages and disadvantages it has.
Self-leveling floors
Self-leveling floors are ready-made compounds that have high plasticity, are able to fill evenly all voids and, by analogy with liquids, spread horizontally. Such products are convenient in installation, since they do not require additional alignment.
The filling in the garage
There are several types of compounds, but all of them can be divided into two large groups - cement and polymer. What kind of floors is best done in the garage depends on how often they will get aggressive substances. Compositions with cement have a very high strength, they are extremely durable and are relatively cheap.
Polymeric compositions contain various substances, which, when hardening the screed, form a plastic moisture-resistant monolithic coating. In some mixtures additives are added, making the finished floor chemically stable. This technology can not be called revolutionary, on the contrary, it has been tested for decades, since polymeric liquid formulations have been used in production plants in factories since Soviet times.
Ceramic tiles and porcelain tiles
Ceramics is one of the leaders among wear-resistant floor coverings. The secret of the success of such a tile is its silicate glaze, which, in fact, is a glass that is famous for its chemical resistance and resistance to abrasion.
Using tiles as a floor covering
The disadvantages are fragility, because when heavy objects fall tile you can split. The quality of the finished substrate is highly dependent on the quality of the intertice joints and the quality of the substrate. Under the tile will have to align the rough surface to the ideal state.
The technology for the installation of porcelain stoneware slabs is the same as for ceramic tiles. Ceramic granite is not inferior to it in strength and durability, but from the point of view of ergonomics it is preferable. The structure of the material is such that the surface will never be slippery. Water flows down on it as quickly, cleaning with solvents and rough mechanical cleaning are allowed. Porcelain can be purchased at a low price, budget items will cost much cheaper than tiles.
Polymer tiles
Durable, easy to install, ergonomic and stable polymer floor has the only drawback - a high price.
Comparison of different types of coatings
From what is better to make the floor in the garage can be solved by evaluating the pros and cons of each type of coverage.
Concrete surfaces and surfaces from moisture-resistant coatings behave differently during operation. In the garage, finished with any kind of tile, you can induce an ideal cleanliness, in which it is pleasant to work and just to be. Concrete surfaces can also be washed, but the appearance is still inferior. Oils and fuel are easily removed from the ceramic, leaving no trace, and the concrete floor remembers such spots forever. Acids do not harm tile or polymer floors, and they destroy concrete, it begins to crumble, local damage occurs.
Mounting technology
Any floor covering is mounted on a concrete base, so the screed device is a preliminary stage common to all types of floors. With respect to garages, the norms used in the construction of industrial premises are valid:
- concrete grade for screed - no less than 200;
- the thickness of the screed layer is not less than 150 mm;
- the reinforcement is produced by a lattice of not more than 50 * 50;
- under the screed is necessarily arranged a sand-gravel pillow;
- on the perimeter along the walls it is necessary to leave a groove for water drainage.
Features of the floors in the garage
Any floor of the above listed will serve for a long time if the garage is heated and there is a positive temperature in it. If the garage is cold, then from the temperature drop, the formation of cracks in the concrete and its rapid destruction can occur. To avoid this, you should abandon the winter washing car in the garage, in extreme cases, thoroughly dry the floor. In dry conditions, sex is not afraid of any differences.
Video: epoxy floor covering in the garage
Ventilation in the garage with your own hands: a diagram, photos and recommendations
Dampness, temperature fluctuations and changes in humidity level, aggressive influence of spilled fuel and lubricants and other peculiarities of garage operation can bring a lot of trouble to the car owner. Therefore, when registering a car in the garage in the list of first-priority tasks, it is necessary to make installation of the floor covering. To evaluate the specifics of the operation of the room and choose the right material will help fascinating acquaintance with the types of technical floor coverings and their characteristics. And if you are going to make the installation of the garage floor with your own hands, it will not hurt to stock up with the working tool and free time in advance.
How to choose a floor in the garage?
In the garage, the car owner has to not only store his four-wheeled helper, but also to take care of him. To do this, the building needs a comfortable microclimate, which can be created through the warmth of the garage and the interior finish. The garage should be started with a floor covering. Due to the specifics of the room, the garage floor must meet the following requirements:
- mechanical strength;
- constructive reliability;
- fire safety;
- moisture resistance;
- immunity to the influence of aggressive chemicals;
- durability.
Floor covering for garage from porcelain tiles
The floor in the garage can be made from various materials. Any of them has its advantages and disadvantages, which need to be taken into account not only when choosing a cover, but also in the process of operating a room.
The following options for arranging the garage floor have been most widely used:
- earth flooring;
Such a floor is not capable of protecting the premises from cold and damp. In addition, the ground floor is not able to resist moisture, nor intensive loads when putting the car in the garage and leaving it. But this is the simplest and cheapest way to arrange the floor - all you need is to level and tamper with the earth inside the garage perimeter.
Earth floor in the garage
- gravel pillow;
Gravel-sand cushion is an improved type of open floor. Such a coating does not stand out either for convenience in use, nor for durability, but it copes well with high humidity and fuel leakage. In addition, the cost of such a floor covering will be inexpensive, and laying it is easy to produce and alone.
Installing the garage floor with gravel
- concrete;
Concrete floor - the most practical and durable option for a garage room. With competent pouring and proper finishing the screed will serve for decades without being exposed to wear and contamination. On the other hand, the pouring of concrete is quite time-consuming, and besides quite an expensive task, the solution of which requires the availability of certain qualifications.
Concrete screed on the floor in the car garage
- wooden flooring;
Wooden floors in garage spaces are installed quite often, although the tree does not have such strength and durability as concrete. In addition, unlike the latter, it is a fire hazardous material, which in addition is of interest to pests. At the same time, the laying of wooden flooring takes much less money, effort and time than pouring concrete screed, and with proper care in the process of operation, such a floor will quietly serve for at least a decade, without delivering the owner of the garage no trouble.
Boardwalk in the garage
- ceramic tiles and stone.
Ceramic tiles and stone have high decorative qualities. They are perfectly protected from pollution by chemicals and are not inferior to concrete in wear resistance and mechanical strength. The service life of the ceramic floor is 25-30 years, and the stone floor is 35-40. The disadvantages of ceramic and stone coverings are impressive cost, as well as the fact that in the process of laying both tiles and stone require considerable skill and patience.
Flooring in the garage of ceramic tiles
Pay attention: Improvements in the internal environment are reasonable to implement gradually. For example, to begin with, the earthen floor can be waterproofed with a thick layer of greasy clay and eventually covered with a gravel-sand cushion. If necessary, on such a floor it will be easy to install a lath for covering it with wooden flooring or to pour a reinforced concrete screed for subsequent tiling.
Calculation and pouring of concrete foundations with own hands
Arrangement of the garage floor of concrete is carried out in several steps:
- Calculation of concrete screed.
- Collection of tools and purchase of material.
- Preparatory work.
- Pouring concrete.
- Leveling and dust removal of the floor surface.
Good to know: After the final leveling and dust removal, it is advisable to coat the concrete floor with a special paint or a layer of sealant. This will protect the material from contact with water and aggressive chemical components, as well as significantly slow down the mechanical destruction of the coating.
Car garage with floor covering of painted concrete
Calculation of concrete screed
Reinforced concrete, used in the construction of foundations and screeds, has a multi-layer structure. In the garage, such a floor covering should be installed on a tamped and waterproof earthen pillow.
The composition of the "pie" of the concrete screed includes:
- sandy (gravel-sand) cushion;
- rough concrete;
- heat insulation;
- waterproofing gasket;
- reinforced screed.
Concrete screed in the section
- remove 20 cm of height for the reinforced screed, crowning the "pie";
- provide for the laying of reinforced concrete on an insulating gasket about 5 cm thick;
- bring at least 15 cm to the layer of rough concrete;
- allocate a gravel-sand cushion laid on the bottom of the excavation, at least 10 cm;
Now you can calculate the thickness of the screed. It will be:
H = h dog. + h black concrete + h par.heat.hydrodol + harm = 10 + 15 + 5 + 20 = 60 cm
If the zero mark is set, it is necessary to lower the level of the ground floor to the depth required by the project, i.e. lower it by the thickness of the concrete screed being built.
Ditching under a reinforced concrete floor in the garage
The bottom of the foundation pit and the gravel-sand cushion under the draft concrete should be thoroughly compacted. To solve this problem you need a plate compactor - a powerful tool that can provide the highest quality of sealing of earthen flooring and cushions. As a result, the risk of demolition of the screed due to seasonal movement of soil layers or a sudden rise of groundwater will be minimized.
Sealing of a sand cushion with a plate compactor
When preparing for basic work, it is necessary to check the laser markers from time to time.
Marking "pie" of concrete with a laser level
To fix the level set by the level, a construction marker and a paint cord are used. The marker must be marked with clear marks indicating the boundaries of the concrete layers, after which they should be connected with each other using a paint string.
Marking of "pie" of concrete by hydraulic level
Please note: When calculating concrete screeds, it is necessary to provide a slight slope of the floor plane (up to 2 cm) towards the sewage lines or drainage system. This will ensure spontaneous removal of liquids from the floor surface.
Tools for laying concrete floors in the garage
To fill the concrete screed in the garage you need to thoroughly prepare. It is necessary to collect in advance all the tools that will be needed in the process of work, and stock up the building materials in sufficient volume to complete the construction.
As for the list of instruments, it should be entered:
- concrete mixer;
- vibration plate;
- welding machine;
- a disk saw with disks for cutting metal;
- scrap, shovel and bayonet shovels, as well as metal buckets or other containers;
- a wheelbarrow for transporting sand, gravel and concrete mix;
- hydro level;
- laser level;
- a painting line;
- rule;
- grinding machine for concrete;
- a drill with a nozzle-mixer;
- plastering spatula, trowel and trowel;
- construction roulette;
- wooden malk for grouting concrete.
Calculation of building materials
Sand, cement and gravel are the main components of the concrete mix. The volume of the last, necessary for filling the screed in the garage, is calculated by multiplying the inner area of the room by the height of the "cake" of concrete. In this case, it is necessary to take into account the shrinkage factor of the material, as well as the volume of the insulation liner and reinforcing skeleton. To the value obtained, another 10% of the stock is added, after which, using the table of proportions of the concrete components, it is necessary to calculate the amount of sand and gravel required for the preparation of the solution.
Preparation of a concrete mix with a concrete mixer
In practice, cement M400 or M500 is used as standard for pouring concrete floors in technical rooms. Reference literature says that the average consumption of dry cement per unit volume of the concrete mixture M150 or M200 is 400-410 kg / m3. Knowing this figure, as well as the proportions of the solution, given in the already familiar table, you can perform a quick and accurate calculation of any of the components of the concrete floor screed in the garage.
Please note: In garages located on a terrain with a high groundwater level, on steep slopes or areas where there is a risk of soil shifts or flooding, it is irrational to fill the concrete screed. The floor in such rooms can be made of wooden planks on a pre-installed supporting frame.
Problem floor in the car garage
Preparation for work
To fill the concrete floor in the garage operatively and, most importantly, without complications and errors, it is necessary to make calculations of construction materials and carefully consider the algorithm of actions. At the initial stage of construction, the first priority task is to prepare a pit for laying an insulating cushion and pouring rough concrete.
As part of the preparation of a garage space for pouring a concrete reinforced floor screed, it is required:

For the preparation of the main material - a concrete mixture - you need cement, sand and crushed stone. In the list of related materials it is necessary to make:
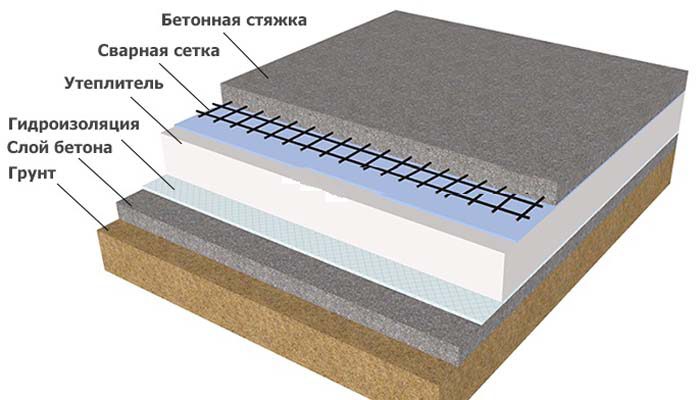
It is useful to know: It is possible to raise the hydro- and thermo-insulating qualities of the gravel-sand cushion with the help of fatty clay, with a dense layer of which it is necessary to lay the bottom of the excavation, without forgetting about careful ramming. When laying a mixture of sand and gravel is recommended to moisten with plenty of water. This will ensure the sealing of the insulation cushion, which will have a positive effect on the quality of the thermal and vapor barrier of the garage floor.
Pouring concrete and laying the insulating layer
If the earth floor in the garage is rammed and laid down by a pillow, you can proceed to pour the rough concrete over the lighthouses. This problem is solved as follows:
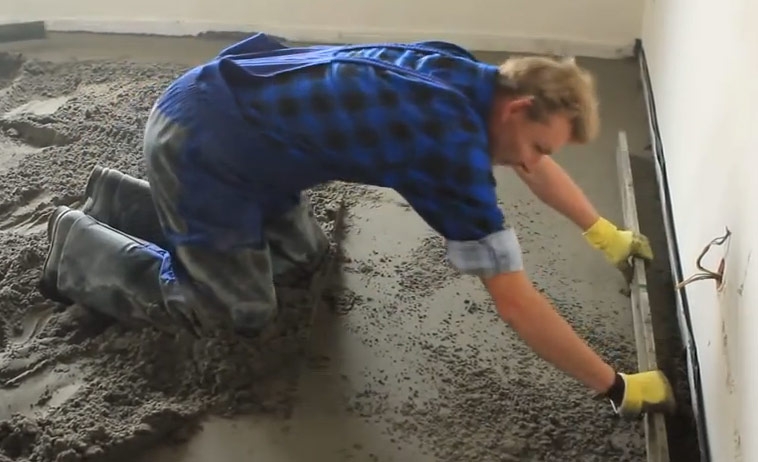
It is important to remember: The screed is poured in one set. You should start from the highest point. The concrete is leveled by a rule in the direction from the far wall of the room. After the filling and leveling of the concrete is completed, it should be covered with a polyethylene film for several hours. After setting the solution after 0.5 hours from the moment of pouring, it is necessary to surface the surface using a wooden mackerel.
How to dust, straighten and finish the finish
After casting the reinforced concrete screed, the face of the latter needs to be leveled. But before it should be carefully inspected for cracks, chips and other defects in order to estimate the scope of the forthcoming work.
Cracking a new concrete screed
Alignment
The surface of the concrete floor can be leveled in one of the following ways:
- Putty.
- Shlifovkoy.
- Milling.
- Self-pouring fill.
Concrete filling is carried out with a composition based on a polymer with the addition of quartz sand. This method allows you to get rid of only minor surface defects, whereas to remove irregularities up to 5 mm deep you will need a mosaic-grinding machine. Unfortunately, with cavities and wave transitions 2-3 cm deep, this technique can not cope, so large defects are eliminated by milling.
The least time-consuming, but at the same time the most expensive way of leveling the concrete floor in the garage is to fill the self-flowing composition. In this case, if the thickness of the finishing layer exceeds 15 mm, it is recommended to use a polymer-cement screed, whereas with an equalization thickness of not more than 8 mm, it is possible to do with cheaper polymerized concrete.
In the presence of critical surface defects and significant differences in height, an additional 1-8 cm thick screed should be made, which not only aligns, but also strengthens the top layer of reinforced concrete. This is done in several stages:
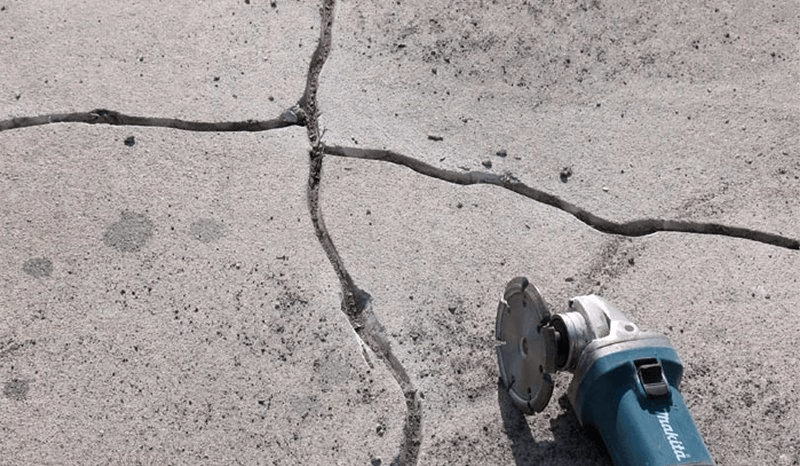
Good to know: The mixture for the leveling screed is prepared in small portions. In the process of pouring air bubbles, large lumps and accidental debris are removed using metal rakes or a shaft with a needle nozzle.
Dedusting concrete screed
Unprocessed concrete is characterized by intense dust formation, because due to the accumulation of frozen cement mills on the surface, the mechanical strength of the floor is significantly reduced.
Destruction of untreated concrete screed
If, when filling the screed in the car garage, do not perform dedusting, this will result in:
- increasing intensity and deepening of erosion of concrete;
- permanent contamination and dusting of the garage;
- the appearance of squeaks and crunch when moving on a floor covering;
- the dust entering the moving and rubbing parts of the equipment and machinery operating in the garage;
- decrease in the comfort of staying in the garage and the appearance of a danger to the health of the car owner.
Dedusting the surface of a concrete screed involves the use of strengthening mineral or polymeric impregnations. With regard to the former, the most common formulations are based on sodium silicate or lithium polysilicate.
De-dusting impregnation on the floor screed in the garage
When interacting with calcium compounds on the surface of concrete, they form a glassy structure that not only protects the screed from destruction, but provides it with additional strength. The disadvantages of mineral dedusting include:
- the duration of the course of chemical processes (from several weeks to several months);
- risk of reverse alkaline - silicate reactions;
- labor input of the composition;
- the need for thorough washing of the screed after soaking.
The most practical, but also very expensive means of mineral dedusting is lithium polysilicate. Its absorption takes place during 10-14 days, after which the screed does not need washing and re-treatment during the whole period of floor exploitation.
To organic (polymeric) dedusting agents are impregnations of the following types:
- acrylic (used to treat screeds with standard strength requirements);
- polyurethane (strengthen the concrete, providing high water-repellent properties and inertness of the material to the effects of chemical reagents);
- epoxy (used in rooms with restrictions on the use of formulations with a pungent odor).
Dedusting concrete floor screed in the garage is carried out in three stages:
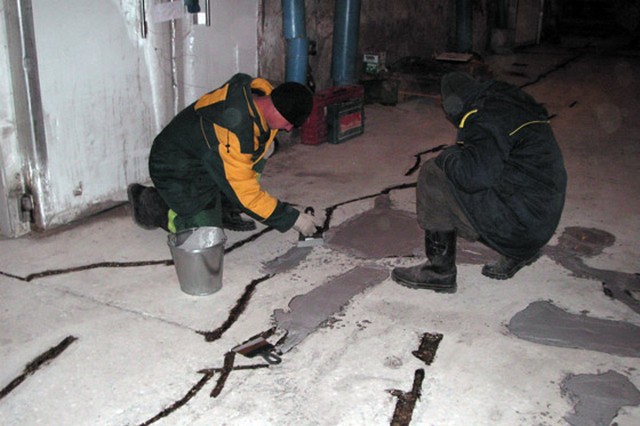
When treating the screed, the de-dusting composition is applied in a spill and evenly distributed over the surface by a brush or rakley.
Concrete screed after impregnation with a dedusting compound
It is useful to know: When using silicate impregnations, the absorption process takes about 40-60 minutes. During this time, the remaining impregnation becomes viscous, so before repeated application it should be diluted with water. After 20-30 minutes after finishing the treatment, the impregnation must be removed with a rubber rake.
Finishing
In addition to dedusting impregnation screed can be covered with water-repellent paint, pre-primed. Staining will eliminate the contact of the floor with moisture and aggressive chemistry, as well as prevent both mechanical damage and premature wear of concrete.
Painting a concrete floor in a garage
With a high intensity of operating loads, it is advisable to protect the screed from cracking and fracture by cutting deformation joints. The latter can perform the following function:
- isolation of the floor from structural elements of the building with the purpose of damping vibrations and chemical interaction of materials;
- isolation of concrete monoliths laid at different times;
- removal of stress due to uneven drying and shrinkage of concrete.
It is useful to know: Cutting of seams is carried out after drying of the screed with their subsequent strengthening and sealing.
Video: Pouring concrete tie in the garage with your own hands
Self-leveling of the wooden floor
Despite the shortcomings of wood as a building material, it is widely used for laying floor coverings, including in garage spaces. The floor, made of this material, absorbs moisture in the air, so that the metal components of the car receive additional protection from rust. In addition, the wooden cover is absolutely safe and much more comfortable to work in the garage than concrete. And, unlike the latter, the wood does not create any dust, and if necessary, allows the operative repair or replacement of worn or damaged elements of the garage floor.
Car garage with plank floor
The choice of method of laying wooden flooring depends on the type of base that is equipped in the room. If a rough concrete screed is filled in the garage, the floor covering is made with a thick (from 5 cm) edging board.
Framework of a wooden floor on a concrete substrate with waterproofing
The latter is laid on the transverse lags of a small section (50 * 50 mm), resting directly on the waterproofing pillow or the walls of the room. Fixation of wooden structural elements is performed by nails, self-tapping screws or anchors. In the event that there is an earth embankment, a clay or gravel-sand cushion at the base of the garage, the wooden floor construction will have to be provided with thick transverse lags (beams) with support on the walls or foundation of the room.
Support of transverse lag on the walls of the garage
Another option for the construction of a wooden floor covering in the garage involves the installation on the earthen or concrete base of bearing columns, on which the frame of the structure will be based.
Support the log of the wooden floor on the bearing columns
Good to know: Before laying a wooden floor, the earth base in the garage room can be filled with rough concrete. However, this option is significantly expensive and very time consuming, so it is rarely used in practice. In most cases, a tamped sand and gravel pillow is used as the substrate for the wooden flooring.
What materials for the construction of a wooden floor choose
If you plan to install flooring in wood in the garage, the first thing to do is choose the right material. The most cost-effective option is coniferous wood. Possessing a relatively low cost, it well resists wear, has little interest in pests and has high mechanical strength. At the same time, a coniferous tree is prone to cracking, and its knotty and resinousness indicate some difficulties in processing.
Lumber for the arrangement of wooden floors in the garage
When choosing a tree for laying the floor in the garage should be guided by the following principles:
- The material must have an optimum moisture content. Too dry a tree can not cope with intensive mechanical loads, and excessively wet with time deforms.
- Planks and bearing lags with pronounced defects - cracks, knots, splits or resin spots - should not be bought even at a discount. Such material will bring a lot of trouble not only during processing, but also during the exploitation of the floor.
- The material is bought with a 15% margin.
- Flooring boards must have a length of at least 2 m.
- As far as possible, the board and timber are taken from one batch. This allows you to count on the same behavior of the wooden floor elements in the process of operation.
- Buy should be polished boards, which greatly simplifies the task of preparing wood for installation and operation of the floor in the garage.
Wooden floor coverings can have a single or double construction. The second option is advisable to apply when it is necessary to insulate the floor, but you can do it with a single boardwalk.
Single and double wooden floor for garage
The optimal solution for the arrangement of wooden flooring in the garage is a pile of spruce or pine boards 36 mm thick and 20 cm wide, or a comparatively cheap but less reliable edging board with a thickness of 40-50 mm.
The paneling is mounted on a mounting plate, the functions of which will be carried out with a beam of 20 * 40 mm cross section.
As load-bearing logs for a wooden floor, it is advisable to use dry beams with a section of 150 * 100 mm.
Bearing beams under the boardwalk
The distance between them at the above thickness of the skin is recommended to be equal to 700 mm. Now, knowing the inner area of the room, it is not difficult to calculate the amount of materials for laying a wooden floor.
Please note: When laying a wooden floor on the logs on a soil basis, account should be taken of the height of the structure. Together with the hydro- and vapor barrier, as well as the mounting plates, it will be about 20 cm. Also, remember that when you support the logs on the walls or foundation of the garage to the useful length of the bar, at least 15 cm is added from each end to which it will be recessed walls.
Tools and related materials
Before you start the work on the arrangement of the wooden floor in the garage, you must collect the tools necessary to perform the related operations. In the list of such it is necessary to include:
- a building level or a tubular hydro level;
- laser level;
- screwdriver;
- a hacksaw on wood and a jigsaw;
- carpenter's hammer;
- carving chisel;
- electric drill with perforator function and a set of drills for metal and concrete;
- screwdriver Set;
- nail;
- ax;
- measuring tape measure and pencil (marker);
- brushes for protective and finishing of wood;
- mounting stapler;
- building knife.
In addition to the main materials, you need to stock up before the start of construction:
- mounting means (self-tapping screws, screws, bolts or anchors);
- emery;
- building gypsum;
- waterproofing gasket and vapor barrier;
- a heater (if necessary);
- means to protect the tree from pests, fire, dampness and rot;
- paint and varnish materials for the finish of the floor.
It is important to remember: If necessary, the construction of a rough concrete screed requires a tool for excavation and preparation of concrete. The volume of the components of the latter is calculated based on the actual floor area of the floor and the required height of the concrete layer. Also, we should not forget about compacting the ground floor and the gravel-sand substrate. They must be performed before the beginning of the basic construction.
Correct installation of the frame
When starting work, it is necessary to impregnate the wood with fire retardant and antiseptic compound. The processed material is placed in the garage. Here he will wait for his hour for several days until the moisture content of the wood stabilizes. But first you should lower the level of the ground floor to the level required by the project, carefully tamper with it and cover it with a sand or gravel-sand pillow. In addition, in the space of the sub-floor, it is necessary to provide intake and exhaust ventilation openings. They are performed on longitudinal walls at opposite corners of the room, while the general exhaust ventilation is output by a separate channel, the outlet of which is located under the ceiling.
Arrangement of natural ventilation in the garage
The algorithm for laying the wooden floor on the logs on a soil basis will be as follows:
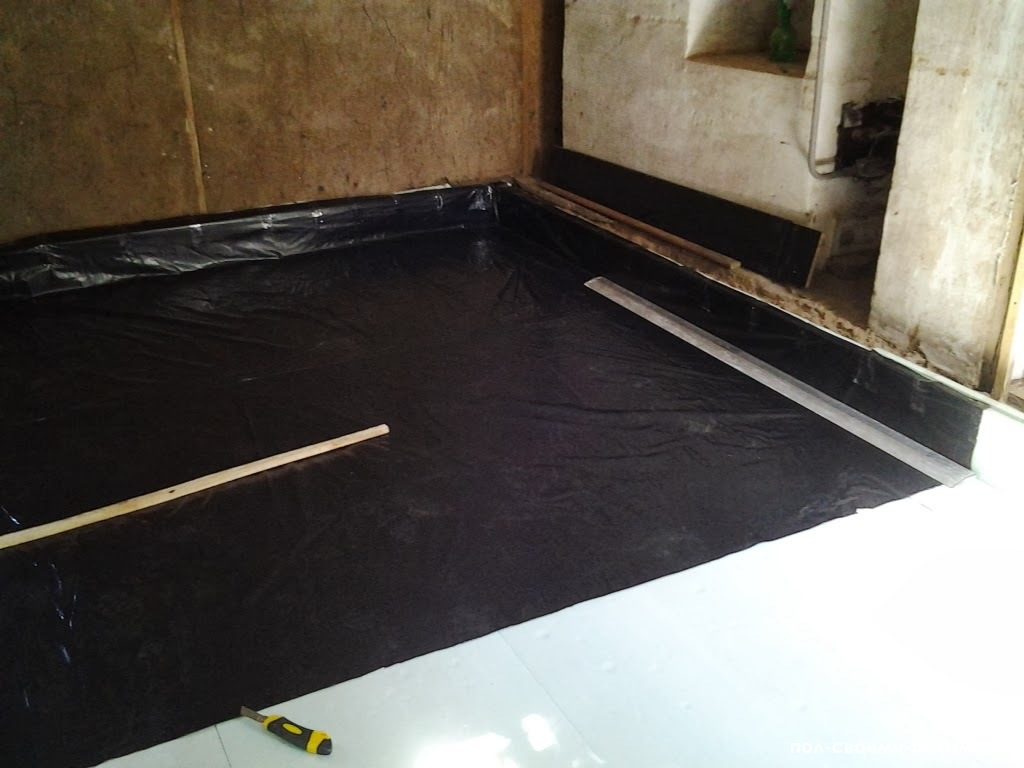
Note: The transverse lugs are laid perpendicular to the movement of the car, and the casing is parallel. Beacons indicating the levels of the floor covering must be set before starting work. It is advisable to stretch the rope tags after mounting the outer crossbars.
Flooring
The finished skeleton of the floor covering is covered with a vapor barrier gasket, which is fixed to the lags with the help of construction staples.
Laying the vapor barrier film under the wooden covering of the garage floor
It is also necessary to think over the filling of voids under the skin. This is necessary for thermal insulation of the floor, as well as for leveling the temperature and humidity under the floor and in the garage. Filling the space of the underground can be directly in the process of installation, for which materials such as expanded clay, sand, gravel-sand mixture or mineral wool are used. With a lack of free time and funds, the event can be scheduled for the near future, but it is necessary before the season changes.
Warming of the floor in the garage with mineral wool
The covering of the floor covering is carried out in several steps:
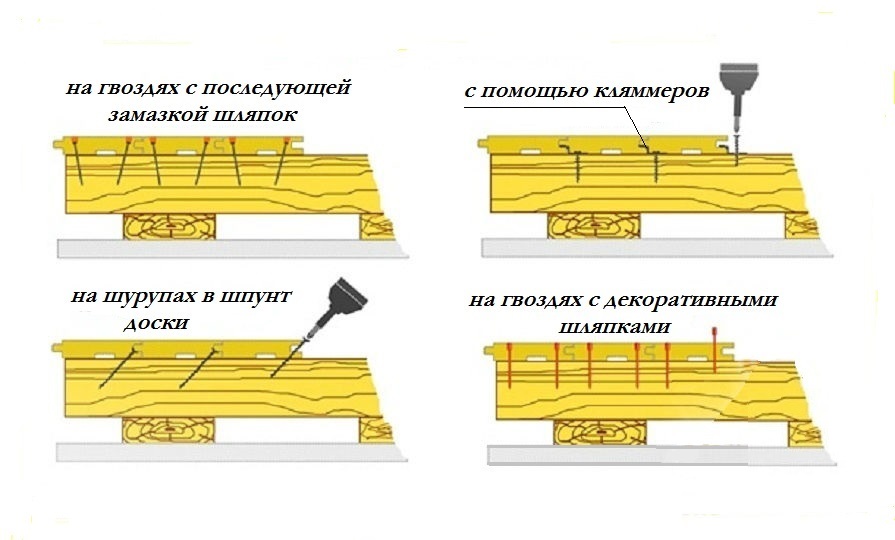
It is useful to know: It is desirable to place the elements of the skin in staggered order, due to which the floor construction will receive an additional margin of safety.
How to protect and process the wooden base
At the end of the installation work, it is necessary to once again treat the front surface of the boards with an antiseptic and soak up the means of protection against pests and fires.
Treatment of the face of the wooden floor with a protective compound
The lining must completely dry, after which it needs to be covered with several layers of varnish or paint. Finishing will protect the face of the floor from moisture, aggressive chemical agents, condensation and mechanical wear.
Wooden flooring of the garage floor after painting
Video: Independent installation of garage floor from a tree
What and how to insulate the floor in the garage?
According to the requirements of SNiP 21-02-99 "Parking of cars" in a car garage it is recommended to maintain a temperature regime of +5 о С and a stable level of humidity. Such conditions can be ensured with the help of high-quality ventilation (inflow of not less than 180 cubic meters per hour), as well as the insulation of the gates, walls, ceiling and floor, arranged in the garage.
The garage is made of metal, insulated from inside with foam plastic
Main characteristics of the heater and its types
The choice of insulation for flooring depends on the type, design features of the latter and, of course, the local climate in which the garage is operated. In any case, thermal insulation should have such characteristics as:
- Non-combustibility.
- Environmental Safety.
- Low thermal conductivity.
- Easy storage, handling and styling.
- Durability.
- Resistance to wear, moisture and temperature changes, as well as other aggressive factors of exploitation, including the development of harmful microorganisms.
Modern insulating materials differ in several categories:
- silicate (glass wool and its varieties, perlite);
- mineral (expanded clay, cement mortars with special additives, mineral wool);
- polymer (foam and its derivatives, polyurethane);
- wood-shaving (plywood, particle board, sawdust and materials on their basis).
Please note: In order to make the right decision on the thermal insulation of the garage floor, you need to carefully study and compare the characteristics of available in the market heaters.
Properties of popular thermo-insulating materials (expanded clay, foam, etc.)
In practice, the most widely used types of thermal insulation, such as:
- expanded clay;
The main advantage of this material is low cost. It has high mechanical strength and low coefficient of thermal conductivity, it copes well with humidity, temperature jumps and chemical reagents. At the same time, expanded clay has a significant disadvantage: the normal thickness of the insulation layer is at least 30 cm, which makes it inappropriate to use it in rooms with a low ceiling. Optimum use of the material for the insulation of concrete floors.
- styrofoam;
A characteristic feature of this heater is the versatility of the application. Polyfoam has a low thermal conductivity, is not afraid of moisture and excludes the possibility of mold development. At a relatively low price of the material, its use makes it possible to significantly reduce the thickness of the thermal insulating liner. Polyfoam is advisable to use for insulation of concrete floor, but it should take into account its shortcomings - low mechanical strength, fire hazard and inability to resist the effects of chemical reagents.
High-density foam for insulation of walls and floors
- polystyrene concrete;
This material is a universal insulation, which can be used as a substrate for both concrete and wooden floors. Its main advantages are high mechanical strength with insignificant thickness of thermal insulation layer, and also enviable resistance to moisture and sudden changes in temperature conditions. Polystyrene concrete shows inertness to chemical reactions and is of no interest for fungal microorganisms. At the same time, it provides a perfectly flat surface of the thermal padding and can serve for more than a decade. Virtually the only drawback of this insulation is an impressive cost.
- glass wool and mineral wool;
These are roll materials belonging to the budget category of heaters. They are universal in use, but they are mainly used for thermal insulation of wooden floor coverings. Glass wool and mineral wool have high thermal insulation characteristics and have excellent vapor conductivity. Meanwhile, they are able to deliver a lot of inconvenience when stacking, and in the process of exploitation can release into the atmosphere harmful components. Due to this, as well as due to the propensity of the material to absorb moisture, the heat-insulating padding requires adjustment of the ventilation gap and reliable insulation from the interior of the garage.
Glass wool for floor insulation
- ecowool;
This material belongs to the class of loose insulation and can be used for thermal insulation of any kind of flooring. Eco-wool is characterized by high thermal insulation performance with a small thickness of the gasket. Meanwhile, this insulation does not tolerate contact with moisture and weakly resists the effects of temperature changes, therefore requires additional waterproofing. Most often, equata is used to insulate wooden floor coverings on a concrete foundation.
Thermo-insulation ecowool for floors and floors
- penoizol;
It is a liquid thermo-insulating material, which is a derivative of foam plastic. Penoizolom can be insulated with any floor covering, including concrete and wooden. It has a low coefficient of thermal conductivity, is not afraid of moisture, no temperature changes, and good air permeability, which contributes to the formation of a comfortable microclimate in the room. The disadvantage of penoizol is a weak resistance to wear, flammability and a very high price.
Thermo-insulating foam insulation
- thermal insulation foil.
This material is supplied in rolls or in the form of solid plates, including a layer of foam or mineral wool. Its main feature is the ability to reflect heat from one side of the thermal insulation sheet and to prevent its leakage from the other. The foamed insulation is impervious to moisture, is indifferent to sharp temperature changes and does not contribute to the development of fungal colonies. The main disadvantage of this material is its high cost. But it is equally convenient for thermal insulation of both concrete and wooden floor coverings.
Foiled insulation based on mineral wool
When choosing a heater for the floor in a garage, the main attention should be paid to four criteria: the index of thermal conductivity, the thickness of the thermal insulation layer, the service life of the material and its cost. The ratio of these characteristics should be optimal for a particular garage space and correspond to the budget of its owner.
Independent insulation of concrete floor
Warming of concrete floor covering in the garage can be performed in several stages, corresponding to the stages of construction of the latter:
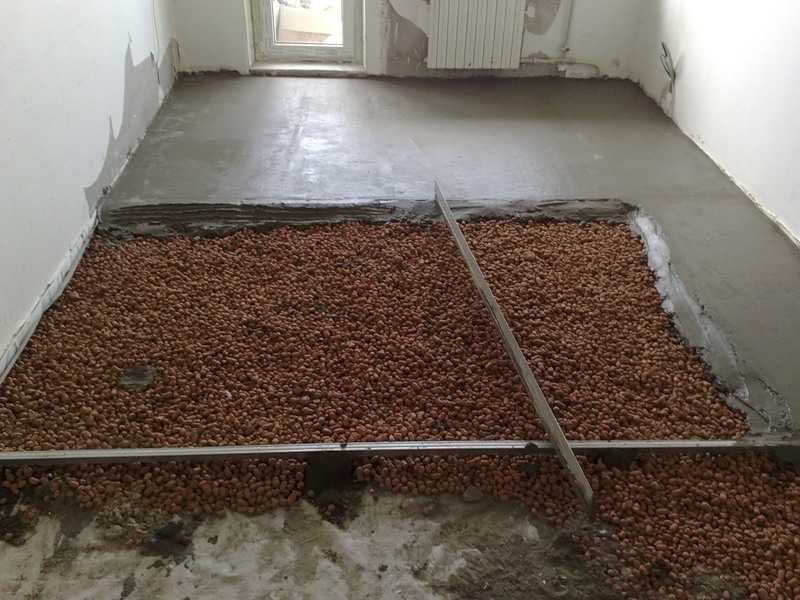
Consider the algorithm for warming the concrete floor at the stage of preparation for pouring reinforced floor screed. In this case, the optimum variant of thermal insulation will be a foam plastic with a thickness of 10 cm and a density of 30 kg / m. Warming is carried out in the following order:
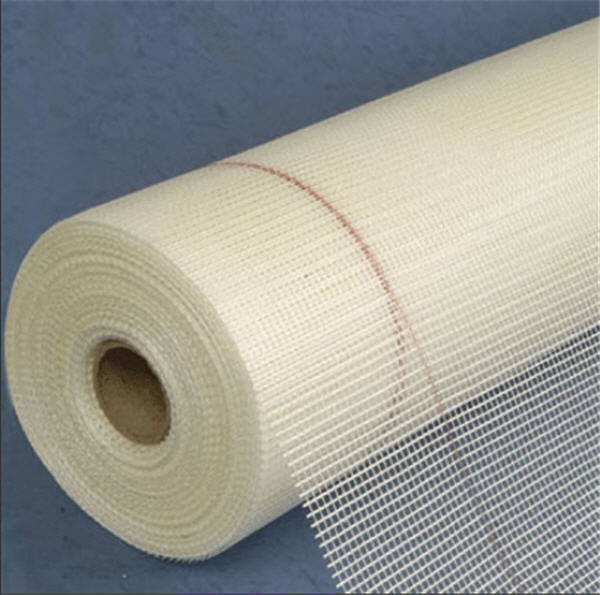
Good to know: To improve the quality of insulation when laying foam sheets, the seams between them are sealed with a mounting foam. When laying the fuser and fixing it with glue, it is necessary to control the horizontal level of the surface of the substrate. Finally, it is possible to increase the strength of the finishing screed filled in the selected substrate by adding the expanded polystyrene pellets to the solution.
We warm the wooden floor with our own hands
Thermal insulation of wooden flooring at the initial stage of its construction is not a difficult task. It is carried out in the standard order: after laying the sand cushion, a layer of waterproofing is installed, crosswise logs are mounted, the insulation and vapor barrier are then laid, and finally the floor is planked with boards. In the event that you need to insulate the finished wooden floor, it will have to be partially or more likely to be completely disassembled.
Analysis of the design of the floor for subsequent thermal insulation
As a material for the warming of the flooring, the most common mineral wool, supplied in the form of plates or flexible mats. In a complex with such thermal insulation should be used high-quality waterproofing, as well as vapor barrier gasket. Otherwise, the insulation will actively absorb moisture, which will lead to rotting of the wooden floor elements.
The method of warming the board floor covering with mineral wool is as follows:
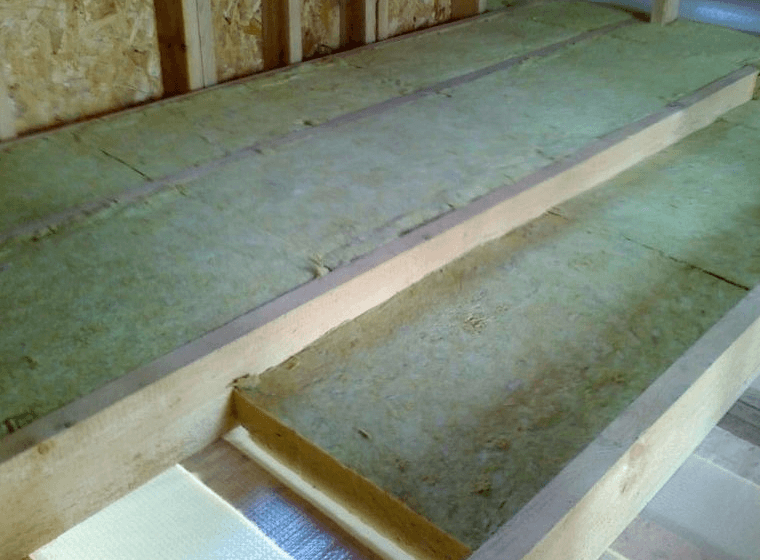
It is useful to know: Mineral wool is of three types - slag, basalt (stone) and glass. Their cost varies significantly and depends largely on the type of material (roll, plate or flexible mat). To insulate the wooden floor is ideal matte material on a basalt or slag base. The upper plane of the mineral wool is marked, which is important to remember when laying.
Competent arrangement of a floor covering in garage will allow to create optimum conditions for storage of a car and daily care of it. The choice of materials for the construction of the floor and its design depends on the conditions of operation of the room, as well as the dimensions and weight of the vehicle. If you comply with the requirements for preparation, laying, hydro and vapor insulation, as well as the finishing of the flooring, the latter will last as long as possible without causing the garage owner any trouble.