Instructions
Disassemble the electrode device. It consists of high-quality welding wire and coating in the form of a coating of a mixture of different powders. The coating is fixed to the substrate with an adhesive. Electrodes for performing special types of welding may not have a coating. In total, several hundred kinds of electrodes are known, which makes it possible to satisfy almost any needs arising during welding, including work with steel, non-ferrous metals and complex alloys.
Choose electrodes, focusing on the upcoming type of welding. For example, to connect low-alloy steels and alloys, stainless steel electrodes with a mixed coating will be needed.
Stop the choice on the electrodes with rutile coating, if you need to weld parts touched by rust. Rutile electrodes are somewhat more expensive than conventional electrolytes, but when used, it is possible to reduce the spraying of the metal, stabilize the combustion and increase the strength of the welded seam. Slag after work with similar electrodes is very easy to remove.
Use ilmenite electrodes to improve the elasticity of the joint. The seam treated with an ilmenite-coated electrode tolerates the ambient temperature drops well. The disadvantage of such electrodes is that they are not very reliable when welding rusty parts.
If you need to connect non-ferrous metals amongst themselves, apply electrodes having a high melting point. The composition of such an electrode includes tungsten and special additives, which have a high resistance to thermal effects.
Pay attention to the color marking. Electrodes with green markings are suitable for welding magnesium and aluminum. The blue marking indicates that the electrode is made of tungsten with the addition of lanthanum oxide. Most often, the last type of electrodes is used to work with copper or alloy steels.
When choosing electrodes, ask the conditions in which they were stored. The fact is that the electrodes have a certain shelf life. If this period is broken, the electrode can not guarantee high quality of the seam. Do not buy welding electrodes , which were stored in conditions high humidity. It is extremely undesirable to buy such products from hand, since the expiration date in this case will be almost impossible to determine.
Transformers have long been a thing of the past. Now they are replaced by welding inverters. They allow you to quickly and efficiently weld metal parts and structures. Typically, inverters are used as power sources for welding machines when conducting arc melting welding. The use of this type of apparatus is renowned for the fact that, thanks to the constant characteristic of the welding current and its stability, an excellent weld quality is obtained, which guarantees a strong and reliable connection of the metal.
What is inverter welding? Strictly speaking, this is a process using a circuit, system or some device that creates an alternating voltage when connecting a DC source. More specifically, this type of welding is a process of working with an inverter, traditionally it is electric arc welding.
The general scheme of such welding consists of a network filter, a network rectifier, a frequency converter, a high-frequency transformer, a power rectifier and a control system.
Of course, to carry out welding of metal of one device is not enough, we need more accessories - a mask, holders and, of course, electrodes. Without them, no work is possible. Electrodes for inverter welding are of three types - carbon, alloy and high-alloy.
The main advantages of inverter welding are:
Light and quick ignition, steady arc burning, good elasticity;
- high-quality welding seam;
- energy saving;
-High efficiency;
- Voltage fluctuations in the supply network do not affect the welding parameters;
- lightness and mobility.
Of course, inverter welding also has disadvantages: the devices used in operation, like any other electronics, do not like water, dust and frosts very much. Therefore, store the inverter welding need in a dry and sufficiently warm room. It is also important to regularly open the case and blow the components of the device with compressed air.
Related Videos
Sources:
- electrodes for inverter welding
Related Videos
In the welding craft, the ability to correctly choose electrodes depending on the type of joints and the grade of steel is a very important professional skill. In this article, we will tell you about the basic types of coating electrodes for MMA-welding and explain how to use them for their intended purpose.
How they work and how they differ
The electrode is a simple metal rod that melts in a lighted electric arc and fills the seam between two parts, simultaneously heating their edges. Covering the electrode, burning, ionizing the medium and supporting continuous burning of the arc. In addition, during combustion, the composition emits gases that displace oxygen from the weld pool and form a slag that floats to the surface of the molten metal and covers it, protecting against corrosion, cracking and other negative effects at the time of cooling.
Understanding the nature of the work of electrodes is very important for explaining such a huge number of their varieties. They differ not only in the strength characteristics of the seam, but also in its position and the type of welding current used.
The difference of the electrodes by the location of the seam
Let us briefly recall how the orientation of the weld pool in space can change and how this affects the welding technique . The most convenient is the lower position of the horizontal seam, which can be flat and angular. In this case, the melt effectively fills the seam and chamfer, and from above a uniform crust of slag is formed which is easily separated. Virtually all brands of electrodes, except for special ones, can be cooked in the lower horizontal position.
Vertical seams are harder to cook. Usually a welding technique is used with a detachment from the bottom to the top. Accordingly, the electrode coating should allow the arc to be ignited quickly and briefly and to effectively guide the molten metal. Also, vertical seams can be cooked without detachment, but for this purpose the coating should be thicker than usual so that a semicircular hole forms at the contact point on the electrode.
The upper (ceiling) location of the horizontal seam is considered to be the most difficult in MMA welding. Without detachment, such seams can not be cooked, they are often welded with a point method with overlapping in 3/4 of the previous surfacing. Covering the electrodes for the ceiling joints facilitates the rapid melting of small portions of metal and the same rapid cooling. Slag from the electrodes also behaves differently. For the most part, it flies to the side (the electrode keeps at an angle) and covers the previous point of stuck. Electrodes for ceiling welding are most sensitive to observing current and polarity.
Type and polarity of the welding current
As is known, inverters have an alternating or direct current output, the latter has a straight and reverse polarity connection. Most electrode welding problems are solved by reverse polarity, at which the electrode is connected to the positive terminal "+" and the part to the negative "-". The peculiarity of the reverse polarity is that the electrons, continuously moving from the negative pole to the positive pole, heat the electrode and its coating, and the metal of the part is heated only by indirect radiation.
With direct polarity, the flow of electrodes is directed from the electrode to the part and heats it directly. The electrode burns more slowly, adding small portions of molten metal to the bath. It is useless to expect that this joint will effectively fill the joint with a wide gap, the direct polarity is used to connect well-fitted parts with a uniform weld thickness. For example, this way it is good to weld metal sheets, the seam is minimally noticeable. Due to the higher temperature of the welding bath with a direct polarity, it is optimal to weld massive parts for which the maximum depth of warming is required.
AC welding is usually characterized by a strong spray of molten metal. The coating of electrodes for AC welding has additives for stabilizing the arc and special alloying impurities, making the melt more viscous. The quality of the welded joint when working with electrodes on alternating current is considered to be the highest for RDS.
Explanation of legend
There are two main specifications, according to which electrodes are marked: domestic GOST 9466 and European standard ISO 2560. Each of them uses its own system of symbols.
GOST
The top line is Т11-XXX-Y-ZN:
- T - type of electrodes, "E" for MMA-welding;
- 11 - the yield strength of the metal in the MPA;
- ХXX - brand of electrodes;
- Y is the diameter of the electrode;
- Z - the purpose of the electrode (Y - low-alloy and carbon up to 60 kgs / mm, L - doped over 60 kg / mm);
- N is the thickness of the coating.
The bottom line is E-AAA-B-C-D:
- E-AAA - type and normative index, determining the strength characteristics of the seam;
- B - type of coverage;
- C - position of the seam;
- D - current characteristics.
- T - type designation of electrodes, "E" for MMA welding;
- XX - the yield strength of the metal in the MPA;
- Y is the index of resistance to impact destruction in MPA;
- SS - type of electrode coating;
- 0 - index of surfacing productivity, type of current and polarity;
- 1 - position index of the seam.
Types of Coatings
The acidic coating (A) strongly melt the weld pool, which causes the metal to crack during hardening. At the moment, it is replaced by rutile-sour.
The main (B, B) coating provides a high viscosity of the metal in the bath and uniform heating of the part. Such electrodes are designed for welding loaded structures, but before use they should be calcined to avoid the formation of pores in the metal.
Cellulose (C, C) coating burns in the arc almost completely, almost without forming slag. This type of electrode is one of the few that you can make vertical seams from top to bottom.
The base of the rutile (P, R) coating is titanium dioxide. Electrodes are optimal for welding with a detachment: they light well and hold the arc, and evenly weld the metal. Rutile coating provides complete control over the welding process and allows varying the length of the arc in a wide range.
Rutile-cellulose (RC, RC) coatings inherit the positive qualities of both types. It is these electrodes that are used for installation in cramped conditions, they leave an aesthetic facial suture that does not require subsequent processing.
Most popular brands
The lower the complexity of the seam, the more comfortable the electrodes are, some literally cook themselves. To such, first of all, it is necessary to carry the famous E46 trademark MONOLITH, they are also ANO-36, popularly called "school" electrodes. They are really easy to cook: the rutile-cellulose coating keeps the arc well even at very low currents, the metal is transferred with small and medium drops, filling the bath well. However, it is not necessary to approach the responsible structures with such electrodes: because of the increased silicon content, the seam loses its ductility and toughness.
Units and joints operating in the open air, including metal frameworks with hinged lining, are recommended to be welded with electrodes, the coating of which contains alloying additives. Such seams have a much greater yield point, and they are exposed to corrosion to a much lesser extent due to a small hydrogen index. An example of such a brand is OK-48. They have a basic coating and melt the metal to a viscous-liquid state, setting the optimum degree of heating, suitable for welding in any position. If you need a provar of 12 mm or more, it is recommended to pre-weld the seam with electrodes with an organic coating such as ANO-7 and ANO-8.
Welding of structures with oscillating types of loads and pressure vessels is performed with OK 61.35 electrodes. Their coating is basic, the metal is very viscous when melting, the seam is practically insensitive to intercrystalline corrosion.
Quickly and quickly to weld any, even the most complex designs from metal, it is possible by means of inverters. These units quickly entered the modern operational processes, because they are easy to operate, while the welded seam is of high quality, smooth and accurate. Of course, the main component of the weld process is the electrodes for welding with an inverter. In fact, this is a metal rod, which is covered with a special material called coating.
Welding electrodes are made of different steel wires, corresponding to GOST 2246-70. Therefore, the electrodes for inverter welding are divided into raw materials into several groups.
- Made of alloy wire. For example, from Sv-08X3G2SM.
- From high-alloyed - Sv-30Kh15N35V3B3T.
- Of the carbon - Sv-10G2.
The brands of welding wire are listed one by one, but their list is wide enough.
As for the protective coating (coating), it is specially applied to the rod in order to protect the weld pool from the effect of oxygen on the melted metal. It is this chemical element that negatively affects the quality of the material, creating oxide films on its surface. It's feathery. The second is the stabilization of the arc.
The protective coating is applied to the welding rod by pressing, so the connection between the two materials is very high. The same coating is divided into four types.
- Basic.
- Rutile.
- Sour.
- Cellulose.
The first and last type is used only for DC welding. The rest are both for constant current and for alternating current.
What electrodes are best for inverter cooking
The electrodes for the inverter are divided into two groups.
- Ordinary, which are used everywhere for any designs. These include the brands ANO and MR.
- Consumables for responsible structures. These include the SSSI brand.
All welders believe that the SSSI brand is very capricious. Not everyone can boil these electrodes, here experience and qualification is necessary. Therefore, it is better to weld the inverter for beginners by ordinary species.
Electrode marks
To answer the question of how to choose electrodes, it is necessary to deal with the marks indicated above.
SSSI
Their main purpose is welding of products from carbon and low-alloy steels. As already mentioned above, they are used to assemble structures, which are subject to increased requirements. Particularly stringent requirements for welds, which must have increased toughness and ductility.
Welding can be carried out at low temperatures. The coating is basic, the current is constant, the polarity is the reverse one. Diameter of the rod: 2-5 mm. Welding seam - high quality, high density. Welded with these electrodes, the structures can cope with temperature changes, bending stresses and impacts.
MR
- MR-3. Used to connect carbonaceous blanks, the joint of which can withstand resistance (temporary) up to 490 MPa. The coating is rutile, the current is variable or constant, the polarity is arbitrary. You can boil the electrode in any position with a reservation. So at the bottom position welding is carried out by electrodes with a diameter of up to 6 mm, in the vertical position up to 5 mm, in the ceiling (top) up to 4 mm. With the help of MR-3, you can brew blanks with rusty coating, contaminated. With them, welding is carried out with increased productivity.
- МР-3С. This is a model that is used for the same purposes as the previous one. The welded joint can withstand resistance up to 450 MPa. The coating is rutile-cellulose, the current is variable and constant, the polarity is arbitrary. Welding position - any. They can even boil wet metals.
The brand of MR consumables for beginners can be called as the best electrodes. It's not capricious, it's easy to transfer the process itself, a little splashing of metal, plus an excellent seam.
ANO
It is necessary to pay tribute to this brand, which all experts consider universal. It is the ANO today that is the most popular brand. If you choose from all the types proposed by manufacturers, then this one.
With the help of these electrodes (welding for the inverter), you can brew workpieces with a thickness of up to 5 mm in different positions, even in a vertical top-down. In this case, the docking of two metals can be: docking, overlapping, angular. To clean the welded edges are not great requirements, you can conduct welding of oxidized surfaces. Produced by them and the root welding of thick blanks. Coating - rutile-cellulose. The current is variable or constant. Polarity is either.
There is in the model range of this type brand ANO-4 with rutile-carbonate coating, which is used to weld critical structures.
OK 63.34
If it becomes necessary to weld two stainless steel blanks, this can be done using an inverter using an electrode from the Swedish manufacturer ESAB. By the way, this electrode can be used to connect products made of structural steel.
The seam from such a consumable is obtained equal to a smooth transition from the base metal. In this case, slag is formed in small quantities, it is easy to beat it off. You can cook any position of joints in metals 6-8 mm thick in root welding. Although the electrode itself was designed to weld thin products from stainless steel. You can connect them butt joints and overlapping. It is also used for multi-layer welding not only in the horizontal plane, but also in the vertical plane.
Carbon and graphite electrodes
The graphite and carbon electrode is rarely brewed by the arc. This type of welding is carried out in shielding gases with filler wire or direct action. In this case, the electrode itself does not melt, the metal is melted, which is welded. With a carbon electrode, the welding is carried out by direct current with direct polarity.
An important component of the welding process is the tight pressing of the edges of the blanks to each other. This can be done by tackers, spot welding or mechanical devices (clamps, clamps, etc.). By the way, this technology can only be used in the lower position.
Welding process
The work of a welder depends not only on the correct choice of electrodes. It is necessary to correctly select their diameter, to accurately set the welding parameters on the inverter itself. Basically, this refers to the amperage. In addition, it will be important to know to which output (plus or minus) to connect the consumable chosen by you.
The diameter of the welding rod should be equal to the thickness of the workpiece, which must be welded. For example, the thickness of the parts to be welded is 3 mm. Hence, it is better to boil an electrode with a diameter of 3 mm. If a thick metal is cooked, for example, 10 mm, then any of the diameters can be used, because the welding in this case will be done layer by layer. But even here it's better to use a thick consumable.
As for the polarity, it depends on the output to which the electrode is connected: to the minus or to the plus. If to a minus, and plus it is accordingly connected to a welded workpiece, it is a direct polarity. If on the contrary, this is the opposite.
What are the differences between the two types of connection? Everyone knows that the flow of electrons (which is also an electric current) moves from a minus to a plus. And that element of the welding process, which is connected to the plus, heats up more. That is, if you change the location of the electrode relative to the position of the connection, you can change the intensity of its heating.
Attention! With an electrode of 3 mm in diameter, it is better to boil a metal with a thickness of 2 mm on the reverse polarity. And the same consuming machine to cook metal with a thickness of 6 mm is better at the direct polarity.
Now, as to the current strength when welding inverter. Usually it is indicated on the package. But you can use a simple ratio: one millimeter diameter of the rod 20-30 amperes of current. Let's face it, the range is wide enough. But it will be necessary to take into account the mode of laying the welded seam. That is, it will be stacked continuously without detachment, or with a margin. In the first case, the calculation takes 20 amperes, at the second 30. Although these are just recommendations, because you need to consider a fairly wide range of welding criteria.
- The fluidity of the base metal, its brand.
- The speed of the hand of the welder.
- The electrode position during welding. For example, in a ceiling position, the current is reduced.
The optimal regime will come with experience. Therefore, the welder should pay attention to the welding bath. It is the indicator of the quality of the selected regime. The correct seam should be even. If a lot of metal formed in the bath, then either the arc is too short or the welding speed was insufficient. If the bathroom got a saddle, then too quickly stitched a seam, or the arc refused length. Displacement of metal in the bathroom in one of the sides indicates that the alignment of the electrode was not strictly aligned. In addition, the current was large.
Choose a good option, which corresponds to the regime and metal, is not always easy. A beginner can not do this, so manufacturers on the package give recommendations. More or less they coincide with the actual ones. But, as was said above, everything will come with experience. We suggest you familiarize yourself with the video - which electrodes should be chosen for welding with an inverter.
In this article we answer questions that arise when choosing electrodes for welding. Different types - dozens and hundreds. Each brand is developed for its own purposes. The value has everything: the material of the rod, its diameter, coating, welding current. Let's understand under what conditions which electrodes are better.
What electrodes to boil inverter
The output of the inverter produces a constant welding current. Therefore, welding requires either electrodes for direct current, or universal electrodes. The further choice depends on the type and thickness of the metal. For example, for household tasks, enough electrodes are 2-4 mm.
What electrodes to cook stainless steel
Stirring is harder to weld than any ferrous metals. It conducts heat worse and is subject to boiling in the weld pool. When overheating, alloying elements burn out, and brittleness increases several times. Ideal, especially for thin-walled steel - welding with a tungsten electrode in a protective medium (argon). This gives a less penetration of the seam.
In arc welding use:
- for food (ordinary) stainless steel - OZL-8, TSL-11;
- for corrosion-resistant steels - НЖ-13, ЦТ-15, ЭА-400 / 10У;
- for heat-resistant steels - OZL-6, KTI-7A, CT-28;
- for dissimilar steels - EA-395/9, ANZHR-1, OZL-312.
What are the electrodes to brew aluminum
Aluminum and its alloys are difficult to cook. Usually one of two methods is used:
- TIG welding requires non-consumable tungsten electrodes.
- MMA welding (manual arc) - using coated electrodes, for example OZANA or OZA.
Also resort to semi-automatic welding (MIG), but then instead of electrodes welding wire is used.
What are the electrodes to cook cast iron
Cast iron is one of the most difficult materials for welding. It is not plastic, when heated in the joint, cracks often occur. Therefore, special electrodes are used:
- ЦЧ-4 - consist of iron with the main coating. Suitable for high-strength and gray cast iron. You can cook only in the lower position, on the reverse polarity current.
- MNCH-2 - used for surfacing of parts, welding of casting defects. Suitable for three types of cast iron: high-strength, malleable and gray. Gives a tight and clean connection. Cook not only in the lower, but also in the vertical position.
- OZh-4 - equipped with rutile coating. Provide a clean weld surface. You can cook in any position, except for the vertical (from top to bottom).
- OZZHN - consist of iron with the addition of nickel. Used for high-strength cast iron parts. Cooked on direct current, making vertical or lower seams.
Welding technique is also important. Cold welding is often used. The seams are made short (25-35 mm) so that the material does not heat up. The second way is directly opposite to the first: joints of blanks are heated to avoid temperature differences.
What electrodes to brew pipes, channels and thin metal
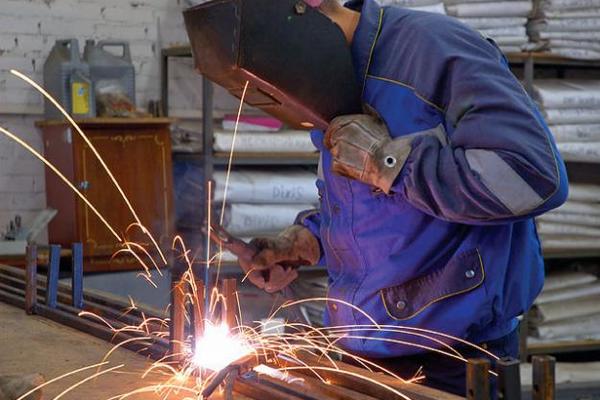
- Welding of pipes is complicated by the fact that you have to cook in different positions. It is necessary to adjust the electrode inclination and the welding speed. The electrode is selected according to the diameter, depending on the thickness of the walls of the pipe itself. Next, you need to consider the pipe material. For steel recommend electrodes OK 53.70 and OK 74.70 (company ESAB). Thanks to a strong seam, they are suitable for high pressure pipes. For connecting copper pipes, either tungsten (non-melting) or melting electrodes, for example UTP 39 (Bohler), are used.
- Welding of the channel (steel rolled) requires a seam of increased strength. The point is that the channel is used as the bearing or reinforcing element of the responsible structures. The thickness of the channel wall can reach 7-13 millimeters. For such massive beams, the SSSI 13 / 55U electrodes are suitable. Welding is possible in any spatial positions. But for thinner channels we recommend universal electrodes ANO-21 with a diameter of up to 5 mm.
- Welding of sheet metal (up to 2 mm) requires accuracy, so as not to burn metal through and through. First, you need an electrode of small diameter (from 0.5 to 2.5 mm, depending on the thickness of the sheet). Secondly, the electrode with a special coating - to slowly melt and stably burn. Among the suitable brands are OMA-2, MT and MT-2. For the most difficult cases, semi-automatic welding using welding wire.
What electrodes to cook with what current
All electrodes are divided into two types: for alternating current and for permanent. Welding on "change" is an easier way, while "permanent" is considered more reliable. Distribution by series looks like this:
- For alternating current - AHO, MP, ES, ESAB OK (also can work on direct current);
- For a direct current - SSSI, OZANA, TSL, OZL, EA, ANC / OZM, etc.
What electrodes to choose for beginners
The initial experience of electric welding is best acquired on welding electrodes of the brand ANO (for example, ANO-21). These are universal electrodes with rutile coating. Convenient in that they allow welding in all spatial positions. Easy to ignite. Metal sprays less, slag easily leaves. Another plus - you can cook wet, poorly cleaned and even rusty surfaces.
By the same criteria, one can advise electrodes OZS-12 or MR-3. The recommended diameter is 3-4 millimeters. Having mastered the work with these electrodes, you can go to OK 53.70, SSSI, LB52U, Kessel and Bohler (the last two are manufactured in Austria and Germany).
For detailed instructions on selecting electrodes, see this video:
Correctly matched welding electrode is 90% success. Even having an inexpensive welding inverter at your disposal, you will be able to get an excellent quality seam. This article is based on the answers to your most frequently asked questions.
What are the types of welding electrodes
Welding electrodes for manual arc welding and surfacing are divided into melting and non-melting (tungsten) electrodes.
1. Melting electrode is a steel wire rod with a special outer coating (coating). Electrode coating performs, as a rule, several functions: it ensures stable arc burning, gas-slag protection of molten metal and alloying of weld metal, depending on the purpose of the electrode. For special electrodes (for welding stainless steel, aluminum, dissimilar steels, cast iron, copper) a rod is used, not of steel, but of a special alloy.
2. Non-melting (tungsten electrode) is an indispensable attribute of argon (or TIG) welding. However, they also differ in their application.
What are the diameters of the electrodes
The size of the electrode is determined by the size of the steel rod. The diameter of the electrodes: 1.6 mm, 2.0 mm, 2.5 mm, 3.0 mm, 4.0 mm, 5.0 mm, and a length of 300 - 450 mm - depending on the nature of the alloying of the steel rod. Electrodes with a diameter of 1.6 mm are available on request; do not find frequent application in the territory of our country.
How welding electrodes are classified
More often welding electrodes classified according to purpose:
- electrodes for welding carbon and low-alloy steels
- electrodes for welding alloy, high-strength and heat-resistant steels
- electrodes for welding high-alloy steels ("stainless electrodes", "electrodes for stainless steel"
- electrodes for welding aluminum and its alloys ("electrodes on aluminum")
- electrodes for welding copper and its alloys (bronze, brass)
- electrodes for welding of cast iron and nickel-base alloys ("electrodes for cast iron", "nickel electrodes")
- electrodes for surfacing and repairing products
- for welding of dissimilar and difficult-to-weld steels
What are the types of electrode coatings
In total, there are four types of electrode coating, but we will focus on the two most common.
1. Electrodes with the main coating ("basic electrodes")
The weld metal has high mechanical properties, including high ductility and toughness, at room and low temperatures, is slightly prone to aging and is resistant to the formation of crystallization cracks. These electrodes are recommended, as a rule, for welding of critical structures and products operating at low temperatures under variable and shock loads
The disadvantages of "basic electrodes" include the tendency to pores in the presence of oil, scale, or rust on the edges of welded parts, with an extension of the welding arc or when the coating is moistened. In addition, the electrodes allow the welding process to be carried out only at a constant current of reverse polarity.
The most popular electrode with the main coating is SSSI 13/55.
2. Electrodes with rutile coating
Electrodes with rutile coating are used mainly for welding structures from low-carbon steels.
Electrodes are distinguished by high welding-technological properties:
- stability of burning arc on alternating and direct current,
- minimal spattering of metal,
- good formation of a seam in all spatial positions,
- good separation of slag,
- excellent welded contaminated, rusty, oxidized surface.
In addition, they provide a good appearance of the seam: the weld metal is not very prone to pores when the length of the arc fluctuates. The most popular electrode of this type is MP-3.
FOR MANUAL ARC WELDING MMA YOU CAN BUY FROM US:
How to correctly choose the polarity of the current when welding with an electrode
Most welding inverter devices for manual arc welding at the output by rectifying an alternating current produce a constant welding current. In this case (using direct current), there are two options for connecting the electrode and the part.
With direct polarity, the part is connected to the "+" terminal, and the electrode to the "-" terminal.
With reverse polarity, the part is connected to "-", and the electrode to "+"
We draw your attention to the fact that there is always more heat on the positive pole than on the negative pole. Therefore, we recommend using the reverse polarity:
- when working with sheet metal, in order to avoid its burnout,
- when welding high-alloy steels in order to avoid their overheating,
- at a direct polarity it is better to cook massive details.
How to choose the required electrode diameter and welding current
There are three characteristics that are very closely interrelated. This is the diameter of the electrode, the thickness of the weld metal, and the welding current.
The diameter of the electrode is selected depending on the thickness of the metal to be welded. When welding steel with a thickness of 0.5 mm to 1.5 mm, manual arc welding with an electrode (MMA) is most often not used, but argon welding (TIG) or semiautomatic welding (MIG-MAG) is used.
It should be remembered that increasing the diameter of the electrode reduces the density of the welding current. This leads to wandering of the welding arc, its oscillation and changes in length. As a consequence, the width of the weld seam increases and the depth of penetration decreases.
When choosing the required electrode diameter, always pay attention to the thickness of the metal to be welded. When welding thin metal with large diameter electrodes, and also in case of welding at high currents, porosity appears in the weld metal.
What are the letters "OK" in the marking of ESAB welding electrodes
Our customers often want to buy ESAB welding electrodes, calling only two letters "OK". We explain that all welding electrodes produced by ESAB (Sweden) start with the letter "OK", in honor of the founder of the company Oscar Kelberg. And then the letters "OK" followed by a numerical designation, consisting of four digits.
We would like to introduce you to the most popular brands of welding electrodes ESAB, which have proven themselves on the territory of the Republic of Belarus:
- Electrodes ESAB OK 46.00 (analogue of MP-3, OZS) - a universal electrode for welding carbon and low-alloy steels ("electrode for steels"), providing an excellent welding seam for AC and DC operation;
- electrodes ESAB OK 48.00, OK 48.04 (analog of electrodes SSSI 13 \\ 55) - for welding particularly critical structures on direct current;
- electrodes ESAB OK 53.70 - specialized electrodes for welding joints of pipes and root pass;
- electrodes ESAB OK 61.30 (analogue of electrodes OZL-8) - Electrodes for welding stainless steel grades 304L, 308L, 03H18N9, 06H18N11, 08H18N10, 12H18N10;
- electrodes ESAB OK 63.20 (analogue of electrodes OZL-20) - Electrodes for welding stainless steel 316L, 03X17N14M2, 10X17N13M3T, 06H19N11G2M2. The electrode is specially designed for welding thin-walled pipes and sheet constructions;
- electrodes ESAB OK 68.81 - Excellent electrodes for welding dissimilar, hard-to-weld steels, as well as steels of unknown composition;
- electrodes ESAB OK 92.60 - Electrodes for cast iron, for welding cast iron with steel;
- electrodes ESAB OK 96.20 - Electrodes for aluminum.
For what you need to calcine the electrodes
The penetration of the electrodes is necessary in order to remove excess moisture from the electrode coating. A high moisture content in the coating can cause such a defect in welding, as the adhesion of the electrodes to the part. Especially this applies to welding electrodes with a basic coating.
If you have opened the packing of the electrodes, then you must either use it completely, or, starting work the next day, ignite the electrodes. For this you need equipment for baking and storage of electrodes.
How to avoid this laborious process? We draw your attention to the electrodes of the Swedish concern ESAB, which packs all special brands of electrodes (for welding stainless steel, cast iron, aluminum, copper) into vacuum packaging ESAB VacPac. Electrodes in vacuum are laid in an internal plastic box and wrapped in a durable, airtight foil. Depending on the type and size, the electrodes are packaged in full, half or quarter packs, the number of electrodes in which is determined from the calculation of the use in the shift. The packages are then placed in a standard outer box. Packaging ESAB VacPac provides an almost unlimited period of storage.
How to choose the right electrodes for an inverter
In order to select an electrode, we determine which metals (black metal, stainless steel, cast iron, aluminum or copper) we will weld? We select welding electrodes in accordance with the type of metal. If there is to be a responsible welding, it is better to stop on high-quality electrodes of imported production. For example, the welding electrodes of the Swedish concern "ESAB" have proven themselves in all areas of industry.
When choosing electrodes for welding carbon steel, we pay attention to the purity of the surface of the metal to be welded. If the surface is rusted, wet, then we use electrodes with rutile coating (MR-3, OK-46.00, OZS-12).
When welding responsible structures, we select the electrodes with the main coating. In this case, do not forget: electrodes with a basic coating require careful preparation of the surface.
Determine the thickness of the metal and select the electrode diameter and welding current correctly.
Correctly selected electrodes, even when working on inexpensive welding machines, will allow you to weld any metal at a high professional level.
If you have any questions, our specialists will advise you by phone:
+375 29 653 48 55 (velcome) or +375 17 241-36-99, 241-78-99
welding electrode, electrode selection, types of welding electrodes, electrode welding, electrode welding, electrode selection, electrode assignment, welding electrodes, electrode selection, universal electrode, calcine electrode, electrode diameter, electrode size, electrode welding, electrode with main coating, electrode with rutile coating, rutile coating, character of alloying, packing of electrodes, electrode coating